「この設計変更によって原価がいくら上がるか分からない」「製造現場で勝手に新しい図面ができている」「リペアパーツをいつまで保管したら良いか分からない」「金型が散在していて結局、新規金型を起こした」。1998年当初、私が日本に『PLM』という言葉を初めて紹介したときから、製造業の課題はあまり変わっていないように思う。
日本の製造業は部門内での最適化が進んできたが、部門間の連携は、いまだに遅れていることは多く指摘されている。大部屋活動やプロダクトマネジャーの設置など、横串を刺す動きは多くの企業に広がってきているものの、いまだに職能別組織に依存している会社は多く、人事評価や機種をまたいだ部品やモジュールの共通化などの点で課題は山積している。
顧客は製品仕様を買っているという原則に立ち返ったときに、QCD情報(品質・コスト・納期)について横串を通して製品を見ることができないのは致命的である。技術経営という言葉が当たり前になった今「売れる製品やサービスをつくることにより儲(もう)ける」ことが経営の基本であり、経営者あるいはプロダクトマネジャーがその仕様・機能(スペック)をマネジメントできることが必要だ。
では、スペックをマネジメントするために何が必要なのだろうか。それがBOM(部品表)の存在である。部品個々の情報を製品あるいはモジュール単位で積みあげていくことで、製品としての仕様を可視化し、部門や企業間でマネジメントすることができる。しかし、単純にBOMといってもそこには難しい問題が存在する。
図に例示したのは一例であるが、同じモノであっても、部門によって視点や粒度、見るタイミングが異なるのが、BOMの難しいところである。製品単位で見ることもあれば、機能単位、モジュール単位、工程単位と異なることもある。また、開発段階なのか、生産準備段階か、量産段階かで欲しい情報も異なるケースがほとんどだ。
そして、BOMを活用するためには、何よりもBOMを正しく維持メンテナンスをすることが肝要である。業務を行う際には必ずBOMに変更を加えなければならず、その情報が前後工程に伝達され、必要な際に必要な精度で必要な情報を取り出すところまでのBOMが構築されている企業はほとんどない。
私は何社もの製造業M&Aを経験してきたが、その際に大きなポイントとなるのが、マスターを統合できるかの観点だ。組織や業務プロセスは併せていくことができるが、それでは単に重複業務の一部が効率化されるのみに留まるためだ。実は、M&Aシステム監査をした際、マスターデータがつながらないことを原因としてM&Aが頓挫したこともある。肝心のマスターデータが統合されなければ、製品のQCDの向上や両社の特性を生かした新しい価値の創造にはつながらない。
BOMの構築において、各社苦労しているが、注意すべきポイントを三つ挙げよう。一つはデータモデリングが不足しているということだ。先ほどの部門によって視点や粒度、見るタイミングが異なると述べたが、顧客ニーズを実際の製品として作り上げる一連のプロセスを可視化し、いくつかのパターンのプロトタイプをつくる必要があるが、これができていないケースが往々にしてある。
二つ目がデータを入力する人とデータを閲覧する人は違うということだ。今までExcelやCADで手元管理していたデータをわざわざリアルタイムで共有できるようにする理由はこのためだ。この点、上流工程からの不満が出やすい。下流工程として、製造工程由来の設計変更を少なくすること、類似モデルでの早期立ち上げなどのメリットを示す必要がある。
最後に最も大切な点を指摘しよう。マスターを最新版に維持する仕組みを業務の中に組み込むということである。このマスターは製品構成や設備マスターが変更になった時だけでなく、特に新しい品番を採番する際に働かせるとよい。特に設計は新規に採番をしたがるからである。これらの3点については、今後の連載の中で詳しく触れていきたい。
山田太郎(やまだたろう)
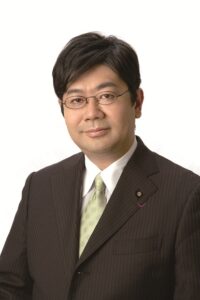
参議院議員
慶大経済卒、早大院博士課程単位取得。外資系コンサルティング会社を経て製造業専門のコンサルティング会社を創業、3年半で東証マザーズに上場。東工大特任教授、早大学客員准教授、東大非常勤講師、清華大講師など歴任。これまでの経験を生かしステーツマン(政治家)として活躍中。