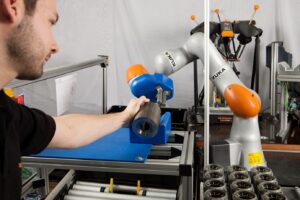
KUKAロボティクスジャパン(横浜市保土ヶ谷区神戸町134、TEL045-744-7531、星野泰宏社長)は、ドイツのシーメンスのデジタルファクトリー(DF)部門モーションコントロール事業部が、同社の協調ロボット「KUKA LBR iiwa」を利用した人とロボットが協調し、高いフレキシビリティを実現した生産システムを導入し、本格的に稼働を開始したことを発表した。同社は革新的なインダストリー4.0を実現するものとしている。
シーメンスDF部門モーションコントロール事業部では、ワークピースを次の工程へ送る、配置するといった手作業で行っていた単純作業を自動化することが長年の課題だった。そこでKUKA Systemsとシーメンス Advanced Technology Solutions部門の共同で、KUKA LBR iiwaを利用したフレキシブルなセルを開発した。
そのセルでは、機械での再校正が必要な部品が“HRCゾーン”に集められ、ネットワーク技術により、各部品の正確な計測と識別情報から、修正が必要かどうか、またシステムに実装可能かどうかを瞬時に計算する。
その後、ロボットが部品を搬送用のプラスチック箱に入れるようになっている。そこでは作業員とロボットが協調して同じエリアで働き、必要に応じて部品やワークピースを取り外したり交換したりもできる。
さらに現在、シーメンスのバートノイシュタット工場では、KUKA LBR iiwaが台車に取り付けられ、さまざまな場所でマルチタスクをこなす頼れるアシスタントとして活躍している。
その一つが、磁性鋼製打ち抜きシートで作られたボディとアルミニウム製支持板で構成されるステーターを、搬送装置からステーターの機械加工用旋盤へと移動する作業を担当している。
また品質検査においても、機械加工を終えた部品をつかんでバーコードをスキャンし、エアブローでクリーニングされたワークピースを傾動装置で計測ステーションへと送る作業を担っている。
この最先端工場で製品の発売および生産技術の開発を担当するウェバー氏は「当初、このプロセスを従来型の産業用ロボットで行うことを検討していた。ところがこの方法では、安全保護のため作業エリア周囲に防護柵を張り巡らせなければならなかった。われわれが求めていたのは、もっとフレキシブルなもので、状況に応じて作業員がいつでも介入し、ロボットの作業を引き継ぐことができる作業環境だった。そしてたどり着いた結論が、このKnightだった。これなら、状況に応じて作業にロボットを利用したり単純に作業から外したりできる」としている。
また、技術開発チームのプロジェクトマネージャのフランツ氏は「HRCの導入も我々にとって目新しいものだった。必要だったのは、開発を徐々に自力で行えるラーニングツールとしてのシステム。KUKAとの共同事業は大成功だった。このソリューションには満足している」と話している。