工場の稼働率は100%が理想だ。現実には難しいが、それでも100%に近づけることが製造現場からの利益創出につながり、価値となる。ダウンタイムを減らす、稼働率を高める、計画通りの生産を行う。これらを実現するためには「設備を壊さない」「壊れたらすぐ直す」の2つの方法しかない。そのためにも万全な保守保全・メンテナンスが重要だ。
しかしながら保守保全部門は人手不足が進んでいる。特に高圧ガス等の専門的な技術が必要とされるプラント業界は深刻だ。
解決策として、AIを使った予知保全等が喧伝されているが、そもそも何千何万とある点検項目すべてにAIを導入していては全くの採算が合わない。その前にやることがある。メンテ項目をそれぞれに対して壊れた時のリスクを重み付けし、その上でどのくらいの頻度で保守するのが適切かを見直すことだ。長く続いてきた暗黙の了解にメスを入れる。適切な保全はそこからスタートする。
産業用ソフトウエア大手のAVEVAは保全業務の最適化に力を入れ、リスク計算から最適な保全計画を実行するRBM(Risk Based Maintenance)を提唱し、それを実現するソリューション「アセットストラテジーオプティマイゼーション(ASO)」を提供している。その取り組みについて聞いた。
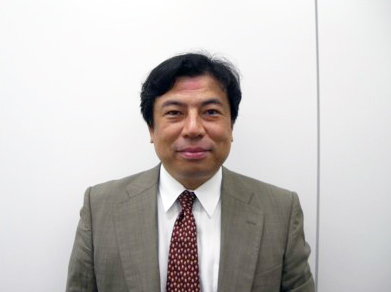
DX時代に求められる新技術「RBM」
産業用ソフトウエア大手
—— 御社について教えてください
当社は1967年創業のイギリスに本社を構える産業用設計ソフトウエアメーカーと同年創業の米国本社のプロセスシミュレーションメーカーを核とするソフトウエアベンダーだ。CADをはじめ設計エンジニアリングツールやオペレーションに必要なソフトウエアを中心に、石油ガス、化学や飲食料品等のプラント、電力や上下水道等のインフラ、造船など大規模設備向けに50年以上にわたって提供してきた。
2019年の売上高は7億7500万。世界40カ国60拠点で5000人以上が働いている。顧客はグローバルで約1万6000社を数え、化学は650カ所超の精製施設、飲食料品では2650カ所、水処理施設は1400カ所、インフラ3200カ所、電力1000発電所などに広がっている。
2018年には世界的な総合電機メーカー大手のシュナイダーエレクトリックグループの一員となった。AVEVAが得意とする設計エンジニアリングと、シュナイダーエレクトリックソフトウエアの操業全体の効率化につなげるソフトウエア、そしてシュナイダーエレクトリックが強みを持つハードウエアと産業用デジタルプラットフォーム「EcoStruxure」を組み合わせ、デジタルツインやデジタルプラントの構築を進め、製造業やインフラのデジタルトランスフォーメーション(DX)、デジタル化の推進を支援している。
デジタル化で増す重要性
—— 最近の保全を巡る環境について
かつてはプラント業界もオペレーターやフィールドの保全技術者が多く在籍し、景気も良かったため人手と費用をかけて手厚いメンテナンスができた。
2000年ころは予防保全(TBM)が主流で、スケジュールを決めて人員を確保し安全を担保してきた。その後、効率化できるだろうということで状態基準保全(CBM)になり、さらにAIを活用した予知保全が広まった。
いまは競争環境が激しくなり、人手不足も進んでいる。またプラントが建設から時間がたって老朽化し、より手をかけなければいけなくなっている。それまでは明確な保全戦略がない企業が多かったが、最近はそれではいけないと考える企業が増えて来ている。
また工場・プラントが省人化・無人化に向かっている。AIを活用してエネルギーやコスト、排出原単位の削減に向けて運転条件を変えていくには現実の製造施設が対応していく必要がある。今後、企業のAI化が進むと同時に保守保全にも注力しないと現実が追いついていけなくなる。そのため当社は保全を重視し、保全業務の効率化に取り組んでいる。
すべての保守手法に対応
—— あらためて、保全の種類について教えてください
保全には「事後保全」「予防保全(スケジュールメンテナンス、TBM)」「状態基準保全(CBM)」「予知保全」があり、さらに当社が力を入れている「リスクベースメンテナンス(RBM)」がある。
事後保全は壊れたら保守をするやり方で、交換部品を持たないのでその分のコストはかからないが、稼働停止が長くかかり、結果として最も大きなコストがかかる。
予防保全は、保守時期はスケジュールで決まっていて、それに基づいて行えう。メーカーが定める交換時期がスケジュールの基準となり、調子が良くても一律交換をするので、結果的にコストは高めになりがちだ。
CBMは設備の状態に応じて保守をするもので、これまでのデータや経験則からしきい値の上限下限が設定され、設備から上がってくるデータがしきい値を超えたらアラートが出て点検となる。データを厳しく見ながら行う手法で、監視型の保全とも言える。
予知保全は、AIを使ったデータ解析で理想的な稼働モデルを作成し、設備からの実測データと付け合わせて監視し、その乖離が出てきたポイントでアラートを出してチェックをする。状態基準保全よりも早いタイミングで異常を検知できる。
RBMは、各点検項目について壊れた際のリスクを数値化し、リスクが高いところのメンテナンスを厚めにし、保全業務を最適化するやり方だ。保全業務に関する人材と費用が限られるなかで、必要なところに資本を集中するという考え方だ。
当社はこれらすべての保全手法に対応する保全システムを提供している。予防保全には「AVENTIS PRO」を展開し、60カ国700社1800サイト以上に導入している。CBMへは、AVENTIS PROの状態監視モジュールとして統計手法を用いて開発したものを展開している。
予知保全は「AvantisPRiSM」で20年以上の実績がある。突発的故障の低減や稼働率と信頼性の向上、エネルギー削減などさまざまな目的に対し、コンプレッサやタービン、ポンプ、モーター、熱交換器など製造装置全体に適応できる。グローバルで約300社で使われている。
例えばフランスの産業ガス企業AirLiquide社では、500カ所のプラントで稼働し50万ドルのコスト削減効果を上げた。アメリカの電力企業Duke Energy社でもサービス維持のために採用され、500万ドルの損失を回避することができた。
リスクを数値化、分類
不可欠なソリューション
—— RBMについて詳しく教えてください
点検箇所について、壊れる可能性が100年に一度しかなく、壊れても損害が軽微なところに1年に一度の点検が本当に必要なのか。保全のリソースが限られる中で業務効率を上げ、事故と稼働率低下を防ぐためにも、保全内容を見直して最適化する必要がある。
従来の保全では過去のデータや経験則から内容が決まっていたが、RBMでは「数値化したリスク」を基準に内容を見直す。プラントにおけるリスクの大きさは「起こりうる頻度×損害規模」の計算式で数値化できる。頻度が多く、損害規模が大きいものはリスクが大きく、その逆であれば小さくなる。
何千何万とある保全項目に対しリスクを数値化し、それをもとに今の保全作業が適切なのか、やり過ぎなのか、不十分なのかを分類する。そこから各項目に対して事後保全がいいのか、TBMかCBMか、予知保全にするか、点検頻度はどうするかなど、内容を変えて最適なところを目指す。これがリスクをベースとした保全、RBMだ。
そしてその保全の最適化を実現するためのソリューションとして当社が提供しているのが「ASO(アセットストラテジーオプティマイゼーション)」だ。システムとコンサルティングのセットで提供し、RBMと保全業務の最適化をサポートしている。
コンサルティングサービスでは、企業のリスク管理について、保守計画・準備体制や保守管理状況のモニタリング、評価体制、再発防止対策、原因有名体制、継続的改善、監査への取り組み体制など14の評価項目で解析し、5段階評価で点数を付けてマップを作る。それをもとに改善点を洗い出し、保守戦略を立てていく。
それと同時にシステムでも保全項目をデータベース化し、それぞれに発生頻度や損害額、現在の保全手法などを割り当てて保全状況を可視化する。そこから現在の保全戦略と最適化の保全をシミュレーションして比較し、自社にとっての最適解を導くことができる。RBMに基づく保全の最適化を支援するソリューションとなっている。
「老朽化」で変わる保全
—— 今後について
これから将来に向けて無人化工場になっていくだろう。その時に保全がしっかりしないと機械が止まって非効率になってしまう。無人化が進めば進むほど保全の重要性は増し、強化しなければならない。
今まではお金をかけてTBMで停止を防ぐので良かった。しかしプラントも50年がたち、定期点検はしていても老朽化は確実に進んでいる。より手厚くメンテナンスをしてリスクを減らしていくという考え方が大事になっている。
保全に対する意識を変えていかなければならない。従業員もテレワークになり、環境が変わってもパフォーマンスを下げないやり方を考え、新しい働き方に対応していかなければならない。人が減っていく環境にあり、従業員と企業のお互いにとってプラスになることを考える必要がある。今まで通りではなく、一人ずつが考えてマインドセットを変えて行く努力をしていくことが大切だ。