製造工場においてローカル5Gによるワイヤレスインフラを構築すれば、電波干渉がなく安定した高速、大容量、低遅延のネットワーク環境が活用できる。また、SIM認証による高度なセキュリティが保てるので、電波を不正傍受されることなく情報漏洩対策も堅牢だ。こうした特徴を持った5Gネットワークを活用することで、ICTの活用やスマートファクトリーへの対応を積極的に進める工場においては、どのような導入効果が得られるのだろうか。工場におけるローカル5Gの導入効果は、「製造工程の効率化」と「作業環境の変化」に大きく分けられる。ここでは「製造工程の効率化」の視点から、ローカル5Gの導入効果が発揮できる活用例を見てみよう。(著:株式会社ミライト)
デジタルツインによるリアルタイム監視でダウンタイムを削減
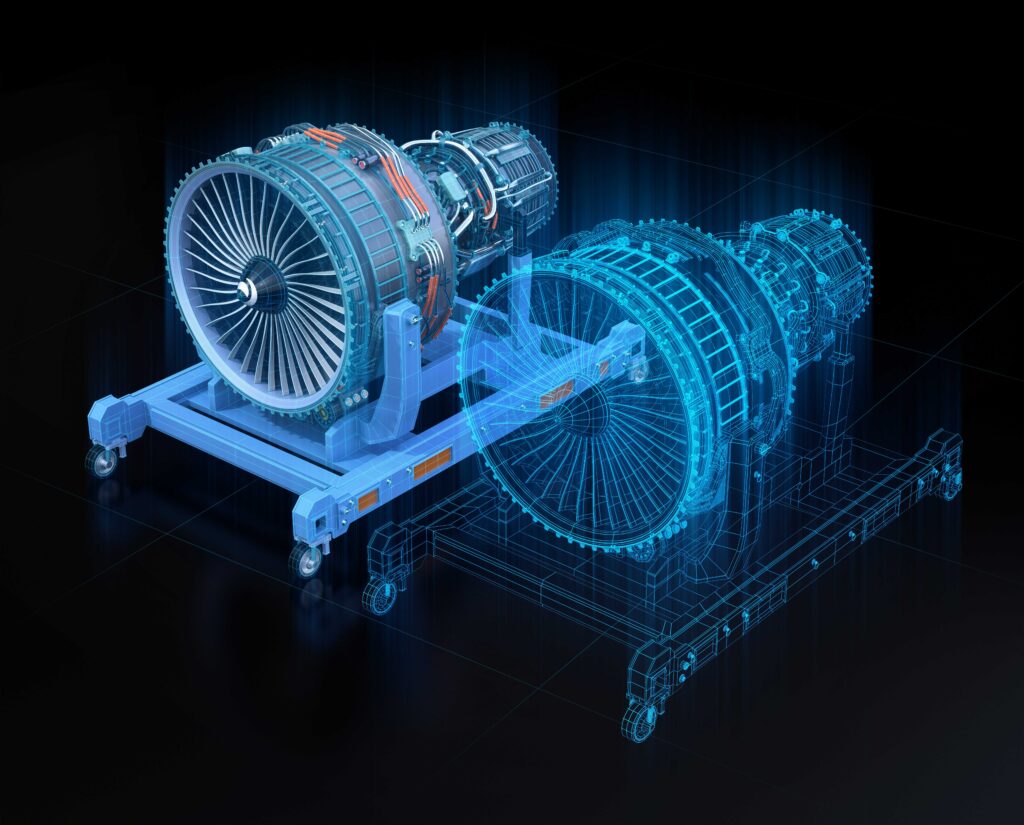
IoT(Internet of Things)やCPS(Cyber Physical Systems)といった最新のテクノロジーを活用してスマートファクトリーの構築を目指す「インダストリー4.0」では、製造装置の各所に設置されたセンサーからのビッグデータがリアルタイムに収集される。そのデータに基づいて、現実世界で起きている事象をサイバー空間で再現する、「デジタルツイン」がさまざまな目的で利用されている。現在デジタルツインは、「CAE(Computer Aided Engineering)」といったシミュレーション解析を行う手法で活用され、製造工程の短縮やコスト削減に寄与している。しかし、インダストリー4.0が目指しているデジタルツインの活用目的は、それだけに止まらない。
インダストリー4.0では、製造装置の状態をデジタルツインでリアルタイムに再現すると同時に、原因不明の振動発生や温度上昇など、センサーからのアラートをエッジコンピューティングによってセンターのサーバに送って分析することで、装置の状態を把握して異常や問題点を予測する。そのまま運用すると装置の不具合が発生すると予測された場合は、運用パラメータをチューニングして装置の負荷を軽減したり、部品が破損する前に交換するなどの対応を促したりする。
単にセンサーからのビッグデータを解析するだけならば、従来の4Gによるネットワーク環境でもデータ通信の遅延はそれほど問題にならない。しかし、解析結果に応じて迅速かつ自動的に対処する仕組みを構築する場合には、不具合の発生が予測され、パラメータのチューニングで対処できることが分かったとしても、通信に遅延が生じてしまえば装置へのフィードバックに時間がかかってしまう。その結果、事前の対処が間に合わなくなって部品が破損してしまい、装置全体に影響を与えてしまうなど、復旧に想定外の時間がかかってしまう可能性がある。
そこで、工場内のネットワーク環境をローカル5Gによるワイヤレスインフラに移行し、5Gの「超低遅延」といった特性を生かせば、4Gの場合にエッジコンピューティングを介したセンターのサーバとの通信で往復20ミリ秒以上かかっていた遅延時間が2ミリ秒前後と1ケタ小さくなる。これによって、ハードウェアトラブルによる製造機器のダウンタイムを極力削減し、製造工程に遅れが出ないようにする。
このように、予知保全には大きなメリットがあるが、ローカル5G導入には、様々な手続きや専門知識が必要だ。免許申請からエリアの構築、運用後のメンテナンスまでを一括して提供するミライトの「ローカル5Gオールインワンパッケージ」であれば、ユーザーは通信建設会社ならではの信頼性と先端技術によるローカル5Gサービスのメリットを享受しつつ、ビッグデータの分析やパラメータのチューニングなど、予知保全の効果を最大化するための業務に集中することができる。
多機能なAGVが工場内を自由に走行
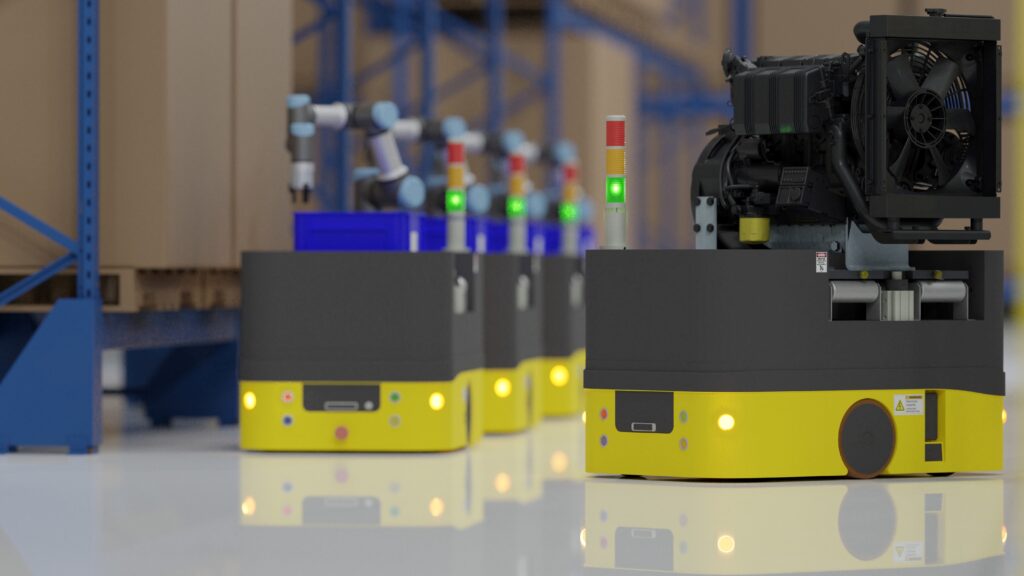
無人搬送車や自動搬送車と呼ばれている「AGV(Automated Guided Vehicle)」は、製造の過程で必要とされる部品や加工品などを運搬するために、日本では20年以上前から中小から大規模工場までさまざまな現場で利用されている。当初は、磁気テープで決められた走行ルートしか動けず、ルート上に人がいたり、障害物があったりするとその場で止まり続けることもあった。また磁気テープを敷設すること自体も、大規模工場などでは大きな負担となり、工場内の柔軟なレイアウト変更を阻むなどの要因となっていた。
最近のAGVは自律移動が可能になり、磁気テープなしで自らルートを判断しながら目的地まで移動できるSLAM(Simultaneous Localization and Mapping)型の普及が進んでいる。こうした最新型のAGVでは、ルートを判断するだけでなく、作業者や障害物にぶつからないように距離を測って避けるなどの機能を実装するため、さまざまなセンサーが組み込まれている。それによって、SLAM型AGVのほとんどが高価格となり、大規模工場で大量にAGVを導入したい場合は、そのコストの負担が課題となっている。
そこで、SLAM型AGVのコントロールをサーバ側に担わせることができれば、AGV本体に搭載する機能を少なくできる。AGVとサーバとの通信にローカル5Gのネットワークを構築し、将来的には5Gの「多数同時接続」といった特性を生かせば、複数のAGVがサーバでコントロールでき、車体の単価を下げることが可能になる。
ワイヤレスネットワークを充実させれば、AGVに新たな機能を加えることも可能だ。例えば、現状のSLAM型AGVはレーザーを使用したLiDARで周囲の情報を取得する機種が多いが、2次元での位置認識となるため、人が頻繁に動き回ったり、障害になるものが増減したりなど、時々刻々と変化する現場への柔軟な対応が難しい。そこで、LiDAR に加えてカメラをAGVに搭載し、3次元での空間認識をサーバでコントロールすれば、より広い範囲での自律走行が可能になる。カメラからの大容量データを、5Gで低遅延にサーバに伝送するのだ。
他にも、工場の生産ラインと物流を連携させ、完成品を倉庫まで運んでパレット積込ロボットに引き渡すなど、AGVの活用にはさまざまな可能性がある。AGVにそうした可能性まで求めるとなれば、サーバからの全体のコントロールは必須となるだろう。また、工場には様々な遮蔽物や障害物があり、建屋内の隅々まで、ローカル5Gのワイヤレスインフラを行き渡らせるのは簡単ではない。ミライトの「ローカル5Gオールインワンパッケージ」では、3Dスキャナや電波伝搬シミュレーションを活用して電波が届きにくいエリアを事前に可視化する。その上で、メタマテリアル技術を適用した反射板、「KLONE (クローン)」を活用するなどの工夫により、省スペースかつ経済的に無線エリアを構築することができる。工場内の特定の場所で電波が届かず、AGVが立ち往生するような事態を避けるためには、電波の専門家によるローカル5G環境の構築が不可欠だ。
AIによる画像解析で製品の不具合をリアルタイムに検出
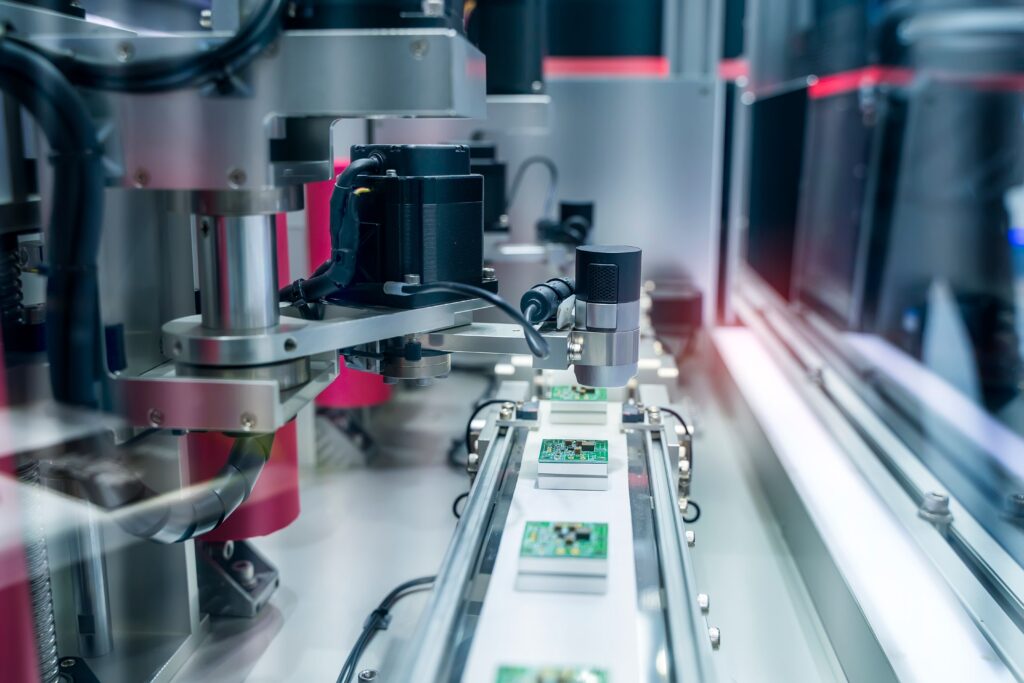
製造業は少子高齢化による人手不足の影響が特に大きく、さまざまな作業の自動化対応が求められている。一方で、多様化する顧客ニーズに応える多品種少量生産や製品の高機能化が進むなか、さらなる作業効率の向上と高度な品質管理への対応も並行して進めていかなければならない。
製造の各工程の中でも、製品の外観を人が実際に見て不具合の有無をチェックする「外観検査」に関しては、作業者の技術や経験への依存度が高く、そのノウハウや技術の継承が喫緊の課題となっている。また、多品種少量生産のプロセスでは製造する製品が頻繁に変わるため、外観検査に関わる作業者も短期間で新しい製品への対応が求められることになる。
そこで、製造ラインに4Kや8Kなどの高精細カメラを導入し、流れてくる製品の画像を熟練の作業者の技術や経験を学習させたAIが解析し、不具合が見つかった製品を振り分ける「外観自動検査システム」の導入が進んでいる。外観自動検査システムでは、カメラで撮影した検査対象の高精細映像をエッジコンピュータに送って解析する。その映像データからリアルタイムで製品の外観上の不具合を判定し、即座に現場の作業者に結果を通知すると同時にその製品をラインから取り除く。判定結果を含む検査画像や製品情報などのデータはセンターのサーバ側で蓄積し、品質管理や分析に活用される。こうした工程にも、高精細映像を「高速・大容量」「超低遅延」で伝送するローカル5Gの通信機能が欠かせない。ミライトの「ローカル5Gオールインワンパッケージ」は、「高精細画像をサーバに伝送するため、ダウンロードよりもアップロード速度を速めたい」というような、個々のニーズに合わせた、柔軟なローカル5G機器の選定やワイヤレスエリアの設計に対応する。
今回の「製造工程の効率化編」では、ローカル5Gのワイヤレスインフラを機械間の通信に利用し、工場内の業務効率を上げていく活用例を紹介した。次回の「作業環境の変化編」では、ローカル5Gが支えるさまざまなアプリケーションを人間が利用することで、人材不足を補ったり働き方改革にもつながるような活用例を紹介したい。
無線エリア構築ソリューション
https://www.mrt.mirait.co.jp/solution/solution32/
https://www.mrt.mirait.co.jp/wp-content/uploads/pdf/20200610.pdf
オールインワンパッケージ