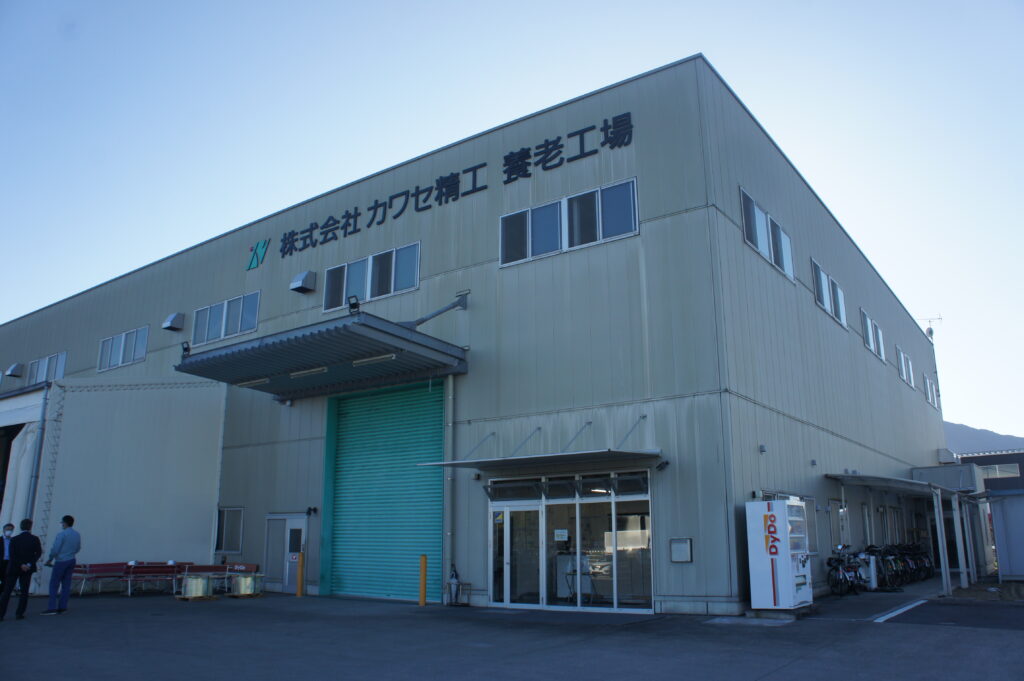
岐阜県大垣市に本社を構えるカワセ精工様は、自動車部品や農機具、事務用品等のプレス加工品を製造・販売する金属加工品メーカー。その製造現場では10年20年もの、最も古いものでは30年以上前のプレス加工機が今も現役で稼働し、ベテランの熟練技術者を中心に、長年積み重ねてきた現場のノウハウ、勘・コツ・度胸で現場を切り盛りする、典型的な地方の中小製造業です。
カワセ精工様ではこのほど、DX、デジタル化の時代の流れに合わせて、現場の見える化に挑戦。このイチからのデジタル化をアドバンテックが支援しました。ここでは、現場へのネットワーク敷設にはじまり、製造機械をIoT化するためのレトロフィット、アナログに慣れた現場の技術者にデジタル活用を定着させるまでの事例を紹介します。
創業60年の地元に根付いた金属加工部品メーカー
カワセ精工様の創業は1963年。当初は金属パイプの旋盤加工工場としてパイプ椅子等に使うためのパイプの切断や穴あけ加工からスタートしました。中部地方は自動車産業が盛んなことから同社も自動車部品のプレス加工を手掛けるようになり、現在では売上の6−7割は自動車向けが占めるまでに成長。さらに金属プレス加工や溶接加工、表面加工、組み立て加工まで自社で一貫して提供し、自動車部品以外にも、事務機器や農機、建機東野金属部品にも取り組み、事業を拡大しています。
古い機械が現役で活躍する本社工場と養老工場
工場は大垣市内の本社工場と、養老町の養老工場の2カ所に構えています。一次加工として養老工場でプレス加工を行い、その後、本社工場に運んで溶接や組み立て、かしめ、塗装、表面処理など仕上げ加工を行います。
養老工場は2013年に設立した比較的新しい工場で、36台のプレス加工機を保有していて、最近導入した300トンをはじめ、昔から使っている10年もの20年もののレトロでレガシーなプレス加工機がズラリと並んでいます。また2000型もの金型を収納する自動倉庫も備えています。
本社工場は、通常の溶接機8台に加え、スポット溶接機10台、ロボット溶接機4台を保有し、旋盤やラジアルボール盤、研磨機、自動カシメ機、各種試験・検査装置を揃えています。
超アナログで非効率も多々ある製造現場
多彩な加工機を揃え、顧客のさまざまな要望に対応できる能力を活かして運営されている本社工場と養老工場ですが、一方でデジタル化や見える化、データ活用という面では遅れていて、現場の非効率の解消や生産性の向上が最大の課題となっていました。
工場にはネットワークは敷設されておらず、生産数や不良数等は毎日、紙の日報に記入。それを管理部門がパソコンに再入力し、そのチェック・振り返りは週や月単位で実施。また本社工場と養老工場は場所が離れていることもあり、それぞれに独立して業務を進め、工程間の情報共有や連携も不足。そのため仕掛かり品の滞留や作業待ち時間の発生、機械の低稼働、納期間近の残業などは日常茶飯事で、その効率化も課題となっていました。
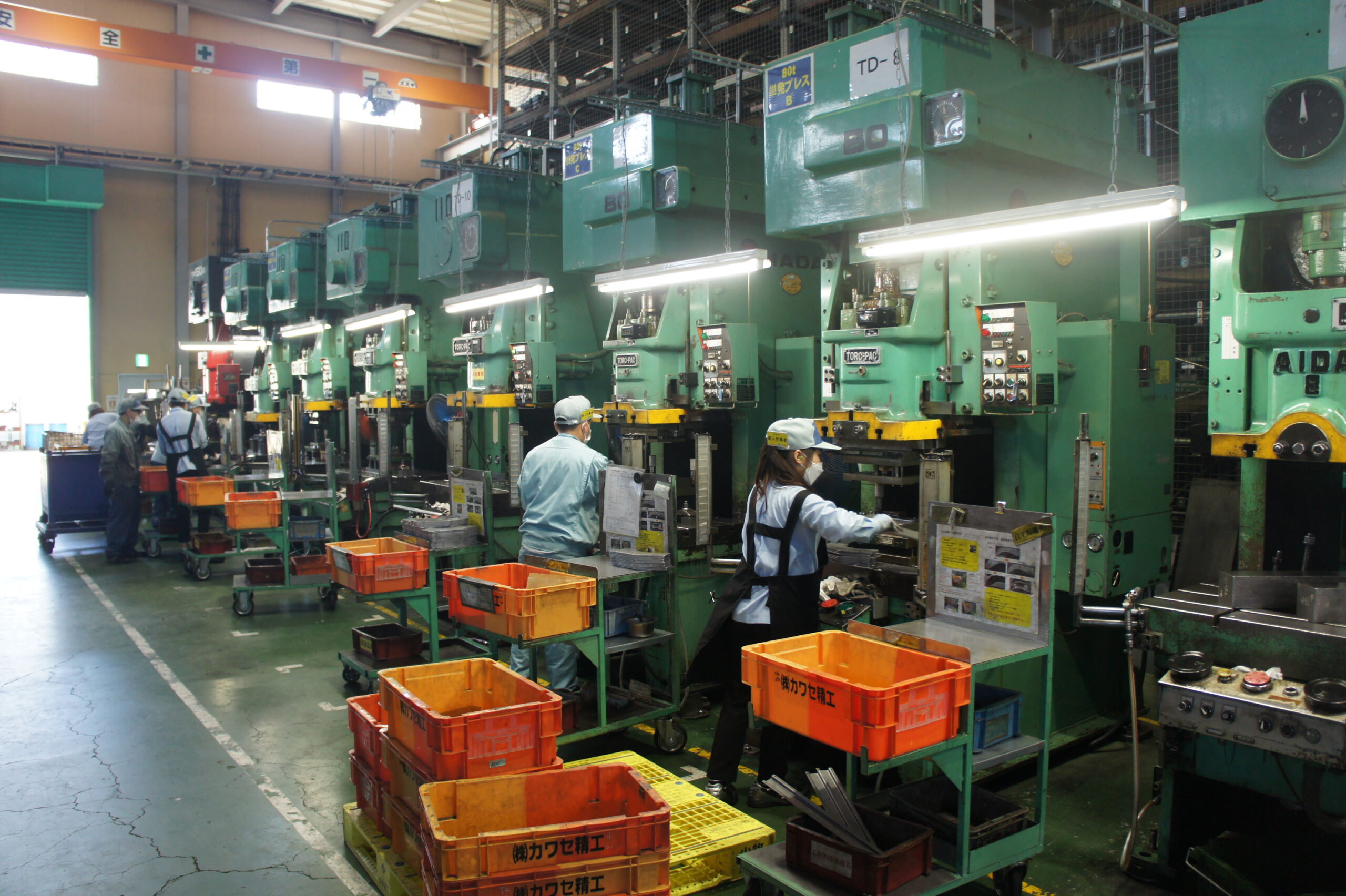
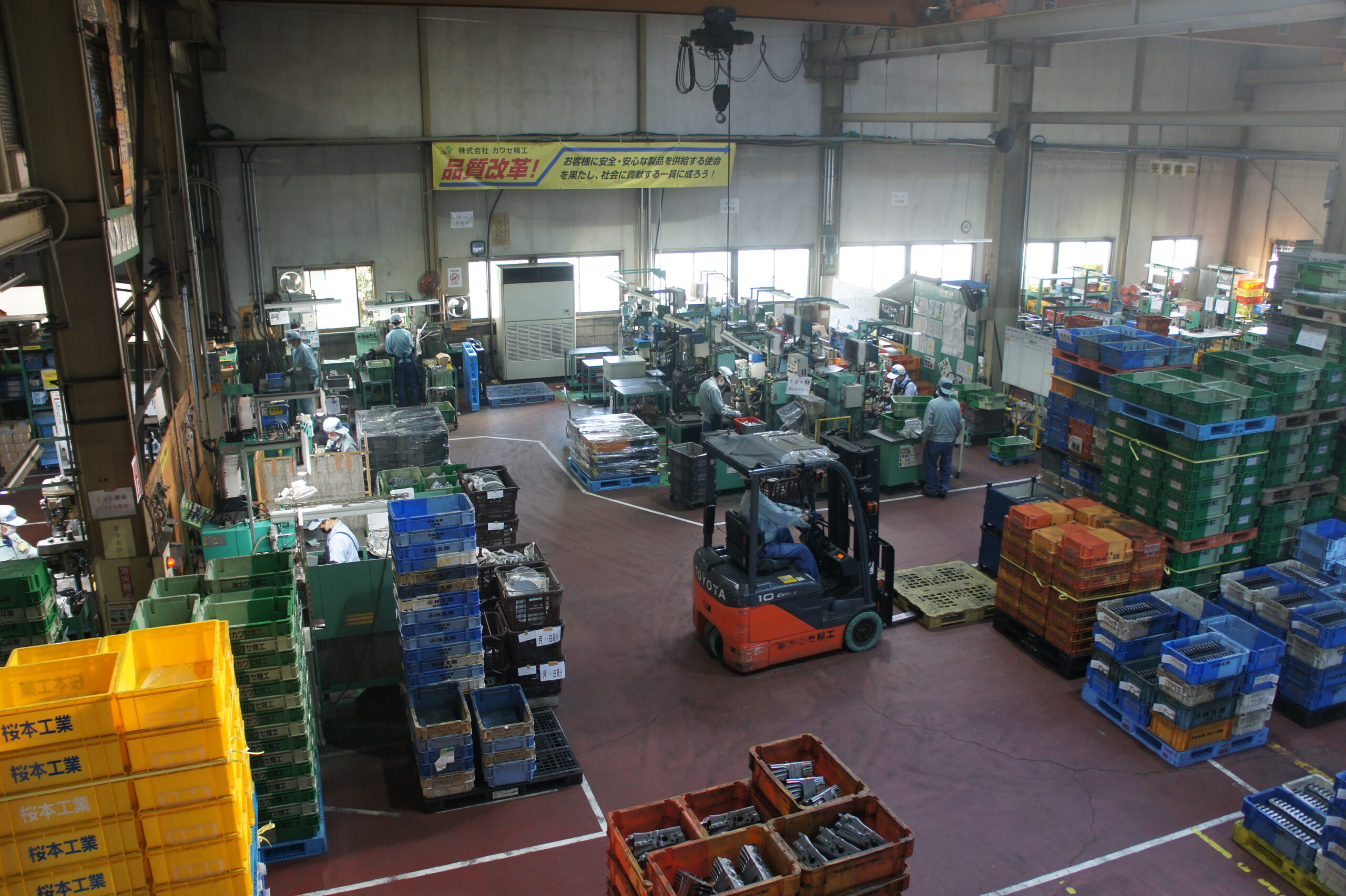
モニター募集・補助金をきっかけにIoT化にチャレンジ
こうした課題に対し、2020年夏頃から川瀬知哉代表取締役社長を中心にデジタル技術で何ができるか、何をすれば良いのかを検討。機械の稼働量と生産数の把握と見える化・遠隔監視、正確な生産計画の立案と実行をやりたいことに設定し、そのための手法を自ら調べたり、動いたりもするなかで、中小機構が運営しているビジネスマッチングサイト「J-GoodTech(ジェグテック https://jgoodtech.smrj.go.jp/pub/ja/)で、アドバンテックが掲載していた中小製造業に向けたIoT、見える化に興味を持ち、モニターとして応募。見事合格し、アドバンテックの支援のもと、現場のIoT化を進めることとなりました。
当初は養老工場の一部の機械、10台ほどの規模でやる想定でしたが、岐阜県が実施している「スマートワーク補助金」に申請し通過したことから、本社工場と養老工場すべてを対象に実行することを決断。一気に工場全部にIoTを導入しスマート化することに取り組み始めました。
初めてのネットワーク構築
取り組んだのは、通信インフラの整備として工場内にネットワーク構築するところからスタート。各作業は独立し、日報は手書き、特に通信を使うこともないことからネットワークは引いていませんでしたが、日報等の入力のタブレット化、電子アンドンの導入、プレス加工機をはじめ各機械からのデータ収集に向けて、今回、初めて工場内に有線LANを敷設しました。
制御盤にIoTモジュールを取り付けて機械から直接データ収集
続いては、データ収集の仕組みの整備。
現場にある機械のデータ収集は、制御盤内に小型のIoTユニット(リモートI/Oモジュール)「ADAM-6051(ADAM)」を設置してリレーと接続し、直接機械から稼働データを収集するようにしました。簡単IoTとしてセンサを外付けしてデータを集めるやり方をしているケースもよく見かけますが、今回はそれを使わずに制御盤から直接データを収集することにこだわりました。
プレス加工機では段取り替えをした時の試し打ち・テストショットを必ず行い、外付けセンサだとそれらもカウントしてしまうので不正確なデータになります。また金型にセンサを取り付けると人の作業エリア内にケーブルが這うことになり、万が一の時にはリスクになります。ADAMを使うことで、制御盤から正確なデータを取ることができ、制御盤内への取り付けなので現場の作業員の邪魔にならず、意識されることもなく、データの質と安全の両方に配慮した最適な形にすることができました。
養老工場のプレス加工機のほか、本社工場の溶接ロボットや各加工機械の制御盤にも同様の形でADAMを設置。スポット溶接機は通電した時を1カウントとし、ロボット溶接は原点に戻ったら1カウントとすることで装置から正確なデータを収集。こうして本社工場・養老工場のすべての加工機からデータを収集できるようにしました。
それ以外のデータ収集は、これまで紙で行っていた人の作業管理、いわゆる日報や作業履歴の入力は、堅牢な産業用タブレット(AIM-68)を採用。現場にタブレットを設置し、各人がタブレットで入力できるようにしました。
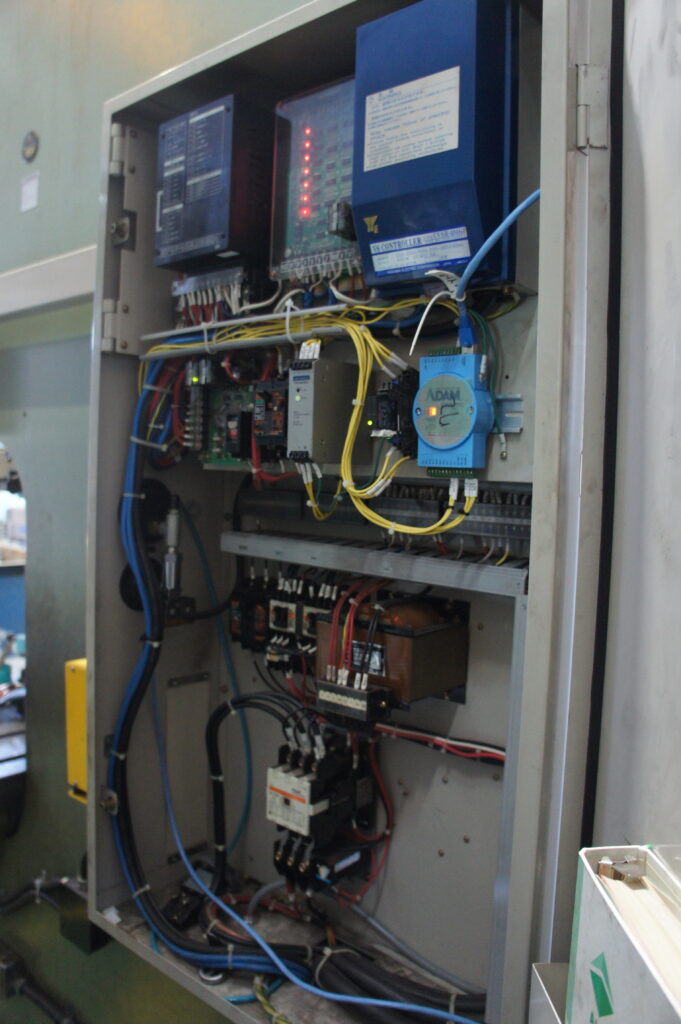
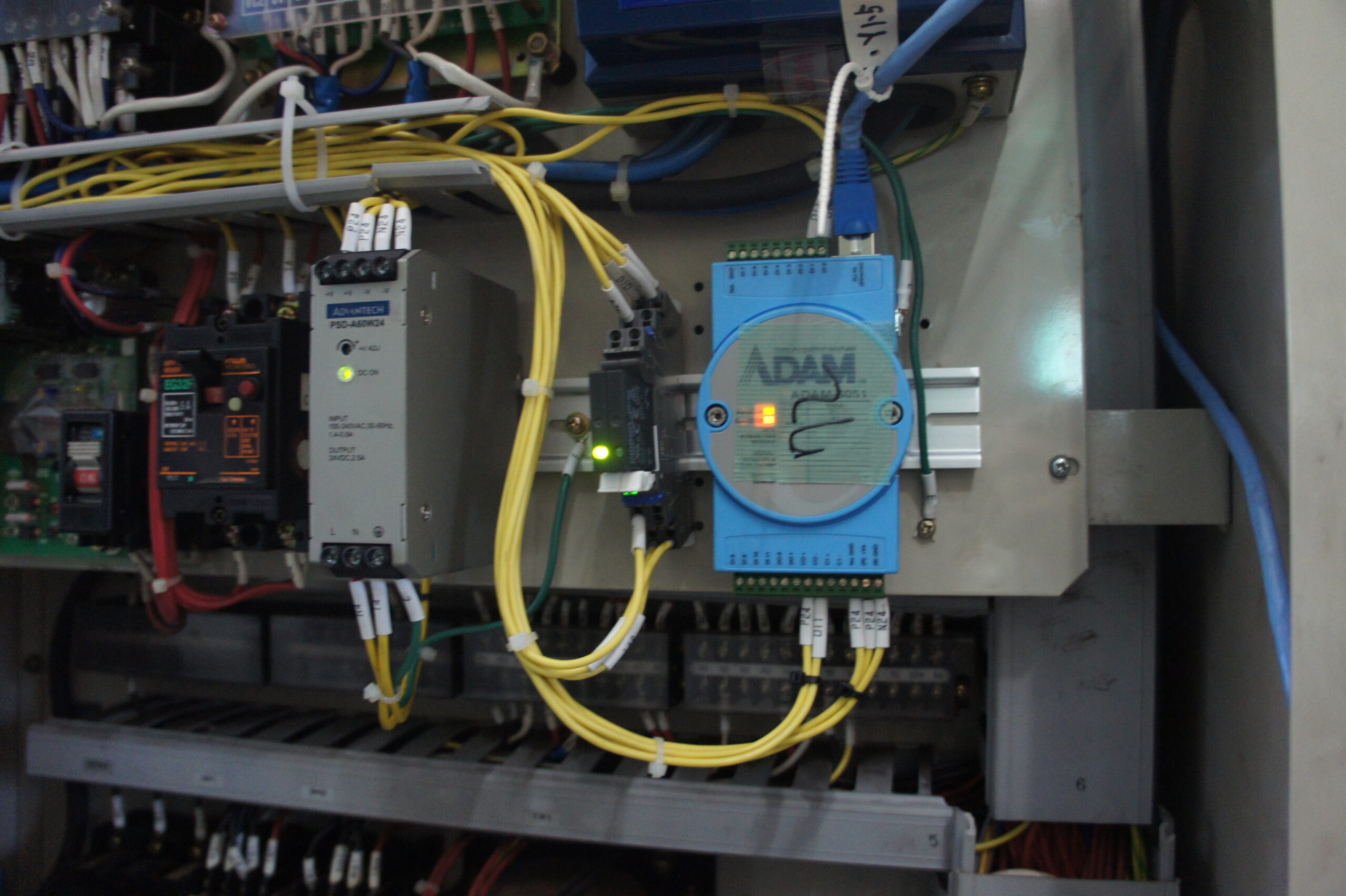
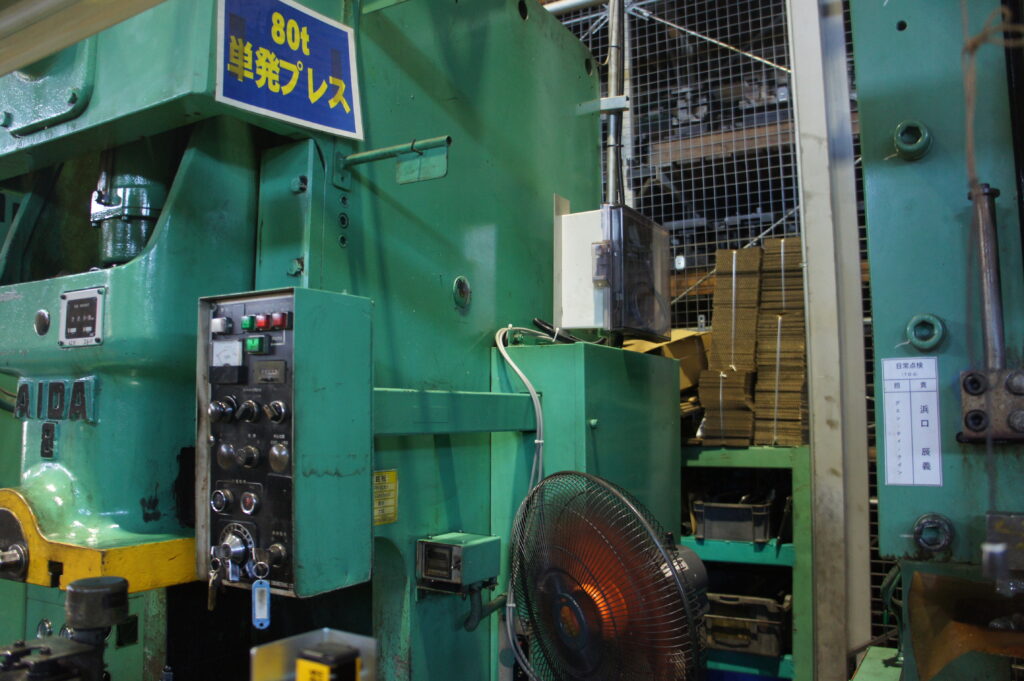
エッジとクラウド活用でデータをまとめて見える化
そして見える化基盤の整備。
各機械から集まるデータは工場のエッジPC(UNO-238)で動くSCADA「WebAccess/SCADA」に集められるようにし、そこからクラウドのIoTプラットフォーム(WISE-PaaS Japan East)に上げられ、本社工場・養老工場に設置されたディスプレイ(電子アンドン)にダッシュボードとして生産進捗や工程管理、各機械の稼働管理など各データが表示されます。事務所のPCからもアクセスでき、事務所、本社工場、養老工場で同じデータが見られるように整備しました。
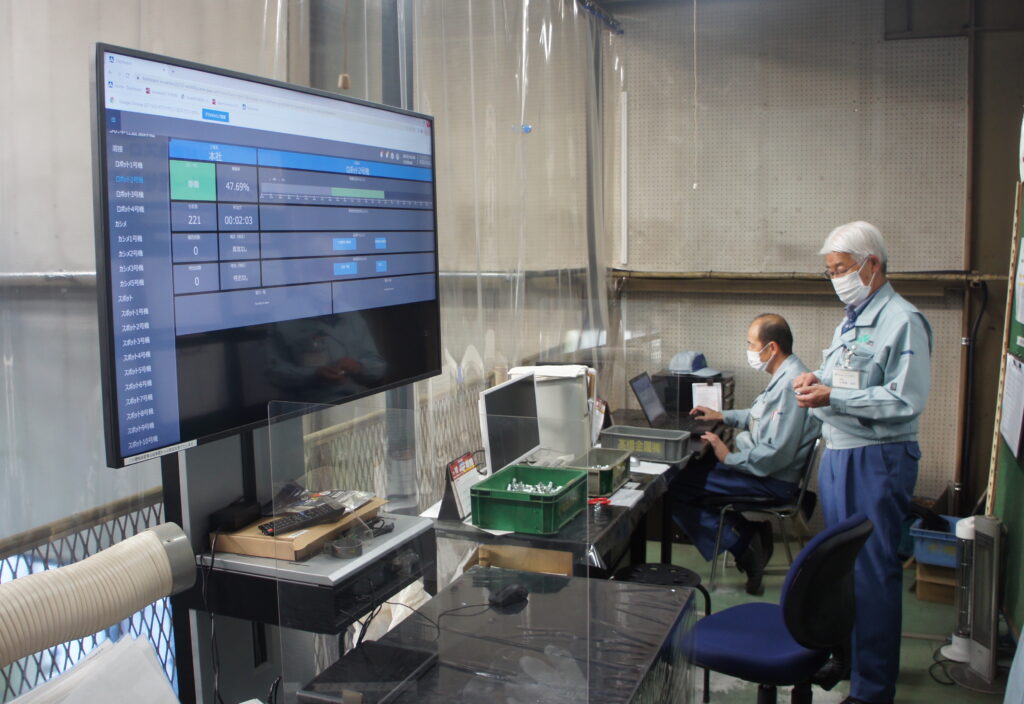
運用開始から半年 成果は上々 社内の雰囲気も変化
工事が完了したのは2022年2月末。現場での運用がはじまって半年超が経過し、開始当初は現場からは「タブレットの使い方が分からない」「IoTや見える化をやる意味が分からない」と不満が出ていましたが、現場の声に合わせてタブレットへの入力をQRコードでできるようにするなど改修を進め、現在ではタブレットからのデータ入力率は80%に達し、ほぼ定着しました。
今はまだデータを貯めている段階としていますが、成果は上々で手応えも感じている様子。「データという事実ベースで現場と話ができるようになったのは大きな前進。またデータの集計に関しても、リアルタイムで見られるので判断や対応も早くできるようになりました」(川瀬社長)。
現場では、本社工場と養老工場がお互いの状況が見えるようになって共通の話題で会話するようになったことをはじめ、機械の稼働率や状態を気にするようになり、良い反応が出ていると言います。また、使われていない設備や稼働率の低い設備が分かるようになってきて、機械の更新や入れ替えの時の検討材料にできそうだとしています。
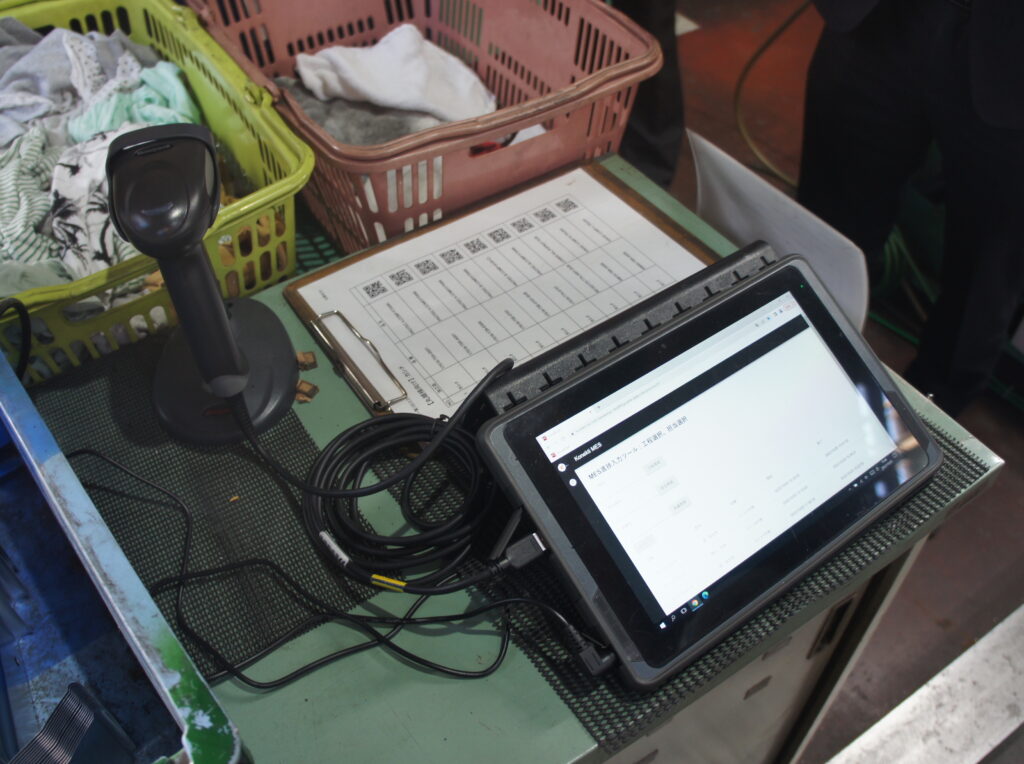
身の丈に合った最適なシステム選び 予実管理の仕組み構築が今後の目標
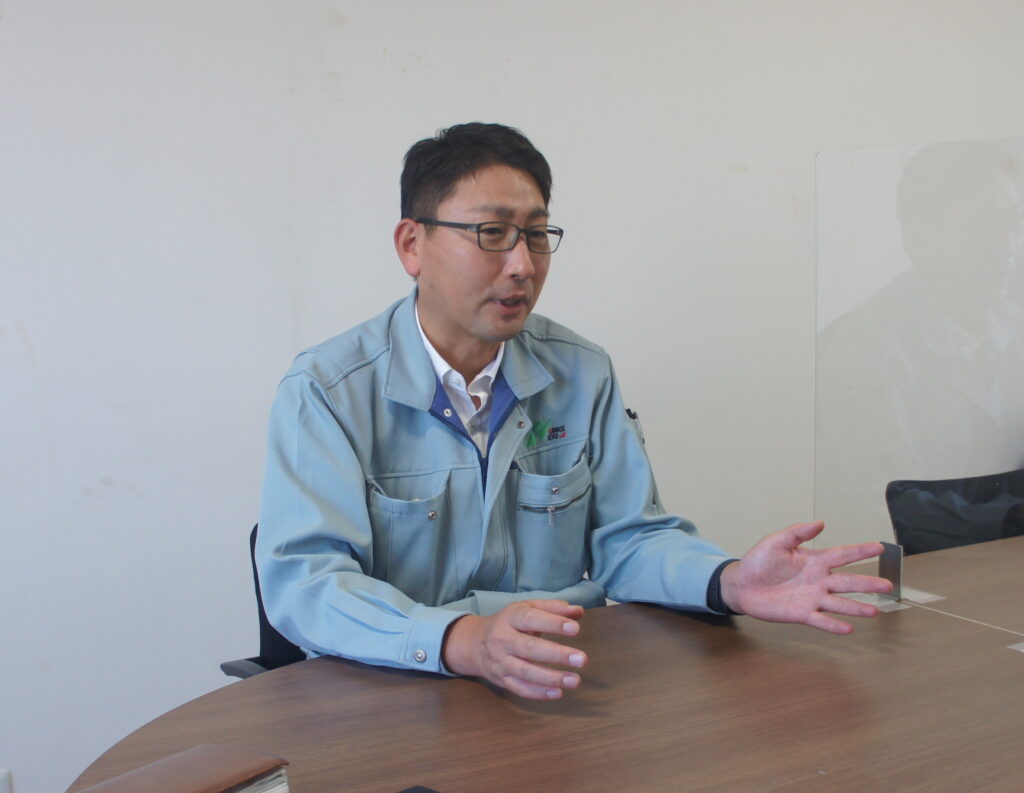
コロナ禍や部材の納期遅延など難しい状況下でのIoT化、見える化に向けての設備投資でしたが、設計から立ち上げ、運用と、これまで大きなトラブルもなく、比較的順調に進んできました。
川瀬社長はこれまでを振り返り「DXやデジタルが話題になってから、ウチでも何かできないか、現場がスマートになったら素晴らしいとずっと思っていて、自らシステムを調べたりもした。当時は大企業が使うレベルの高額で大規模なシステムか、センサを取り付けて簡易的にやるシステムの両極端しか選択肢がありませんでした。そのなかでアドバンテックが提案していたシステムは、すでにIoTのプラットフォームがあり、スモールスタートできるというのに惹かれて声をかけ、結果として大成功でした。補助金の申請もサポートしていただき、当初想定していたものから規模が大きくなってスケジュールはとても厳しいものでしたが、アドバンテックさんと工事会社にはとても頑張っていただきました。コロナ禍で社内の雰囲気も沈むなか、こういう時だからこそ前向きに新しいことに取り組み、風を吹き込もうという思いで取り組み、今はとても満足しています」としています。
また今後については「生産管理システムを入れ替え、現場での生産実績と生産管理システムを連動させ、予実管理をしっかりやれる仕組みを整えようとしています。これまでは多品種少量生産のため、各製品にどれくらいの工数と時間がかかるかの正確な把握ができておらず、むやみに受注を増やして現場の残業が増えたり、パンク寸前になることもありました。いまはIoT化によってそれが少しずつ分かるようになり、適切な営業と生産ができるようになってきました。見える化によって現場のさまざまなものが可視化できました。見えるようになることに悪いことは何もありません。これからもさらに進化させていきたいと考えています」と話しています。