連載の初回記事「中小製造業こそマスカスタマイゼーションに取り組むべき理由」(リンク埋め込み)で示したように、大量生産(マスプロダクション)を手掛けながら各顧客の嗜好の違いに応える受注生産(カスタマイゼージョン)を組み合わせることがこれからの中小製造業の生き残りには欠かせません。単純な製品の大量生産だけでは中国や東南アジアからの輸入品に勝つのは難しくなります。そこで付加価値額を最大化する戦略が欠かせないのです。
しかし受注生産を大量にこなすだけでは、生産工程が煩雑になって製造コストが跳ね上がってしまいます。マスカスタマイゼーションの導入にはデジタル技術を使った効率化が同時並行で欠かせません。筆者が勤める東洋電装(広島市)では経済産業省のDX支援プログラムも活用しながら、ITによる中小企業の改革を後押ししています。デニムメーカーのカイタックグループ(岡山市)に伴走した事例を紹介します。
■新ブランドで生産量を平準化
江戸時代から繊維産業で栄え、国産デニム発祥の地として知られる岡山。綿織物、縫製、染色、色落ち加工など関連企業が集積します。カイタック様はこの地で1948年に創業。売上高は約800億円と地元での存在感は大きく、技術力にも定評があります。そんなカイタック様も国内市場の縮小や新型コロナウイルスによる需要減少といった課題に直面していました。
カイタック様はこれまで、実店舗で販売する2~3万円ほどの高級デニムブランド「YANUK(ヤヌーク)」が主力でした。ただコロナで外出機会が減った結果、デニムにこだわる層の買い替え需要が大きく減退。販売量が落ち込んで工場の稼働率も低まってしまいました。
そこで自社の通販サイトで販売する新たなブランド「岡山DENIM」を立ち上げました。10種類ほどの様々な形のデニムで、お客様がある程度までデニムの形を指定できるセミオーダーメイド方式です。価格は6000~7000円くらいでヤヌークよりも求めやすく、新たな顧客層を獲得しました。コロナの影響が比較的小さい日常使いの品として浸透していきました。一本の利幅はヤヌークに劣りますが、まとまった数量が出るので工場設備の稼働率が安定しました。
ただ売り上げが伸びるほどに工場では「嬉しい悲鳴」ともいえる新たな問題が起きていました。新しいブランドを従来と同じ工場内で生産したため、新旧ブランドが同じ生産ラインに混在。生産管理が煩雑になりました。デニムは裁断、縫製、染色、加工、完成検査など、アパレルのなかでも工程が多いことで知られます。
■エクセル職人が限界に
従来は機械の稼働予定や商品ごとの生産フローの管理は、特定の担当者に任せきりでした。注文の状況に合わせる形で、担当者がエクセルで作業員の配置や機械の稼働スケジュールを計算していました。まさに綱渡りといえる状態で、特定の「エクセル職人」の技術に頼っていました。
そのうちに商品数が増え、列や関数を追加して管理はますます複雑に。その日の稼働予定を組むのに精いっぱいで、全体の生産性向上にまで目をやる余裕はありませんでした。そんなときに東洋電装の代表とカイタック様の工場長がイベントでお会いしたことでプロジェクトが動き始めたのです。
カイタック様はそれまで全くDXに取り組んでいなかったわけではありません。岡山県の補助金に採択されるなど、生産工程の一部ではデジタル技術を取り入れていました。
ただこれが大手IT企業のサービスを一つの生産工程に入れ、結果としてロボットやAIによる効率化で「2%歩留まりが改善しました」といった目先の成果で満足してしまうケースが多いのです。カイタック様に限った話ではありません。
東洋電装は自社の制御盤の生産工程を根本から変えた経験があります。細かい部分のDXに取り組んでも、継続的に投資し続けてリターンを生めるかもわかりません。まずは自社の業務フローを棚卸しし、現状をもとに「マスカスタマイゼーションに必要なDX」とは何なのかを突き詰める必要があります。
■毎日いるはずが…気付かなかった稼働率の違い
カイタック様で稼働率の停滞を招いていたのは「洗い加工」と呼ばれる、デニムに風合いを出すための機械を使う工程です。ここで前の工程から流れてきたデニムが滞留していました。そこでまず生産プロセスを分析するため、広島工業大学の協力を得て「動画撮影による作業の徹底的な解剖」をしたのです。筆者を含む東洋電装のメンバーも現地に入りました。
洗い加工の工程にカメラを合計5台設置して20日間の動きを撮影。「作業員が特定のエリアに入ったか」「2台ある窯(機械)がそれぞれ稼働しているか」についてログを取得して抽出しました。
工場の間取り上、2台の窯の大きさ・処理能力が違います。一方は大きくて一度に100本のデニムを洗えるのに対し、もう一方で一度に洗えるのは50本です。作業員たちは無意識に100本入る機械を優先し、50本のほうの窯は停止時間が長く、その時間は100本の機械の数倍に上ったことが判明しました。
動画で撮影してログを分析するというアナログな手法ですが、問題の把握には大変効果的でした。従業員も効率を最大化していると勘違いしている人も多くいましたが、頻繁に出し入れが必要な機械を無意識に避けてしまっていたんですね。これまで使っていたエクセルを改良することで、双方の稼働率を最大化することが重要だと気付くことができました。片方の機械の稼働が一定時間止まっている場合、ランプなどでアラートする手法もこれから考えられます。
動画検証では、熟練と非熟練の作業員で大きく効率が違うこともわかりました。「なんとなく」の職人技で片づけられていた差が、データとしてしっかり見えるようになりました。これは若手作業員に何が違うのか、説得力をもって教えられるデータにもなります。結果をもとに動画マニュアルを作成し、作業員のレベルを一定以上に引き上げることにもつながりました。全体としての作業効率は20~50%、向上できる見込みです。
このように、DXを導入する前段の「課題把握」が適切にできていないと、効果的な投資ができないといえるでしょう。
■出荷前検査を自動化、1本あたりの時間を5割短縮
出荷前に採寸して、サイズが基準内に収まっているかを確認する「完成検査」にもAIを導入しました。これまでは人がメジャーで採寸し、紙に記入して記録を管理してきました。サイズや色、デニムの形などSKU(品目数)も膨大で、非常に多くの手間がかかっていました。ここに台の上にデニムを広げれば上からカメラで撮影し、結果をAIが分析してくれる自動検査システムを取り入れました。検査にかかる時間は従来の1・7分から1・15分に短縮でき、記録もデータで簡単にさかのぼれるようになりました。
カイタック様の取り組みを通じて、DXの前段に業務を棚卸しする重要性をお分かりいただけたと思います。生産性が高まったことで従業員の残業も減りました。
次回は広島の伝統産業である熊野筆を取り上げます。百貨店などで売られる高級化粧筆で、その加工技術はまさに職人技の集合体。生産工程にどうデジタルを組み込んだのか、解説していきます。
【著者】
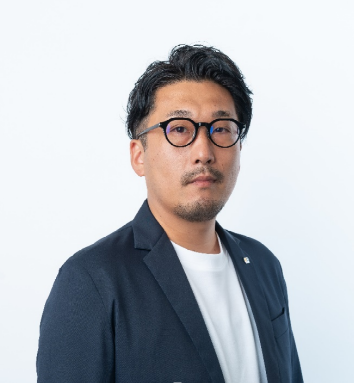
越智 稔(おち みのる)
東洋電装株式会社
制御盤システム事業 事業部長
1984年愛媛県生まれ。制御盤の設計としてキャリアをスタートし、13年間エンジニアとして国内向けだけでなく海外向けのプラント関係制御設計及びシステム開発経験がある。PLC-HMI-SCADAの開発経験も多く、ロックウェル・オートメーションやシーメンスの開発経験と複数カ国の現地でのコミッショニングを経て技術力を高めた。更に欧州向けのIEC60204-1に準拠した設計によるCEマーク取得パネル、UL508Aに準拠したUL認証パネル設計を多く行った経験がある。現在は制御盤製造の事業運営と自社DX推進及び中小製造業のDX推進をサポートする新規事業を産官学連携で立ち上げ、システム開発統括及びフィールドサポートを行っている。