本連載ではこれまで、東洋電装が他社のものづくり企業のDXを支援してきた事例を紹介してきました。今回は東洋電装自体がどのようにDXを進めているのかを取り上げ、読者の皆さんの参考になれば幸いです。
製造業に限らずどんな業種でも当てはまると思うのですが、文房具や印刷紙、トイレットペーパーなど会社として必要な備品がありますよね。東洋電装では、その在庫管理・発注に関して拠点ごとに担当者を割り当てていました。本来の業務の合間に備品棚をチェックしてもらい、なくなりそうなものがあれば商品名や個数をメモ。それを総務部に渡して注文してもらうという流れでした。
こう聞くだけでも何か非効率そうですよね。まずこの備品管理の業務が特定の担当者に依存していることが問題でした。もし担当者の本来業務が立て込んだ場合、発注が遅れて備品切れを起こしてしまいます。かといって備品棚のスペースには限界があるため、一度あたりの発注量を増やすことも難しい。ちなみに製造業における在庫運用もほぼ同じオペレーションです。
■非エンジニアが40時間でアプリ開発者に
そこで発注業務を誰でもできるようにしようと、内製アプリを立ち上げることにしたのです。開発担当者に任命したのは、総務部に勤める従業員。アプリを開発した経験もなければ、ITに特別強いわけでもありません。まずYoutubeなどを活用し、Microsoftのアプリ開発ツール「Power Apps」の使い方を勉強しながら開発してもらいました。プログラミング作業なしでも開発可能なノーコードのツールで、開発工数が少なくて済みます。シンプルな機能のみを求めるアプリであれば、特別な知識はいりません。40時間ほどでアプリができました。
新たな備品発注の流れは次のように構築しました。
①棚にあるそれぞれの備品の近くにQRコードを印刷したシールを貼る
②備品の減りに気付いた社員がスマホのアプリでQRコードを読み込む
③QRコードによって商品ページに飛ぶ
④発注個数を選んで確定する
⑤発注情報がTeamsで発注担当部門に届く
⑥発注部門が決裁して注文を完了する
商品ページでは、いつどの量を発注したのか履歴も表示するようにしました。二重発注を防ぐことやトレンドデータによるネクストアクションにつなげるためです。気づいた社員が手を動かす仕組みなので社内の善意に頼る部分はあります。でも皆さん、トイレットペーパーがなくなるのは困りますよね。製造業における在庫部品等も同じことが言えます。
このように属人化(カスタム)されていた仕事が誰でもできるようになる=「マス」化されるという意味では、マスカスタマイゼーション(少量多品種生産)だと言えます。私が重視する概念です。
この備品発注システムはまだ進化させる構想があります。AIに備品が減るペースを学習させ、AIが判断した適切な周期で発注する仕組みです。開発段階ですが、オフィスの備品にとどまらず、工場の製品・部品の在庫管理などいろいろなところへ応用できそうですよね。
■20近くのアプリを自前で開発
現場の細かい改善において、ITベンダーに新しいシステムを発注していると中小企業はそれだけで赤字になるかもしれません。ただでさえ原材料費や資材が高騰する世の中です。社内の人にノーコードのツールを勉強してもらい、簡単なアプリは内製化するだけで経費を使わずにデジタル化はどんどん進められます。
東洋電装ではこのように現場の日々の業務から着想したアプリを数か月で8つ開発・運用しており、開発段階のものも含めると20近くに及びます。同じ人に開発を委ね続けるのではなく、やったことがない人を優先的に選ぶようにしています。そうするうちにそれぞれ得意作業みたいなものが生まれてきて、お互いに質問して高め合う好循環につながります。今ではノーコードの担当者は10人以上います。
従来では考えられませんが、工場の現場事務所でデジタルによる効率化を目指してアプリ開発方法や機能について雑談が繰り広げられている現場は素敵ですよ。どんな会社でもそうなることはできます。
「中小企業あるある」のような話になってしまいますが、「自社の業務プロセスは極めて特殊で、改善の余地は少ない」と思い込んでいる会社がほとんどです。でも内情を見ていくと取引先が固定化され、仕様が特殊なだけで業務を分解すると意外にそうでもない。シンプルなアプリで効率化できる部分はたくさんあります。
最後にひとつ、東洋電装が進めたDXのケースを取り上げさせて下さい。ある顧客向けの制御盤製造作業を動画で撮影し、作業者の手の動きをログデータ化して分析しました。どの工程にどれだけの時間を費やしていて、どういう導線で動いたか、作業手順にムラがないか、またそれは作業者によって違うのか。まさに作業工程の「デジタル解剖」です。
■特殊品のプレッシャーが原因
制御盤は量産品である「標準品」と、特定の顧客向けにカスタマイズした「特殊品」があります。特殊品といっても、実際に図面を見るとほとんど標準品と変わらないものもあります。動画分析によると、「ほとんど特殊ではない特殊品」にかかる組み立て時間は1時間54分と、標準品に比べて32分長いことが分かりました。
なぜほとんど違いがないのにここまで遅くなるのか。作業手順を追うと特殊品では作業中に逐一、タブレットで指示書を確認しながら組み立てていました。標準品と変わらない製品でも「特殊品だから」という一次情報によるプレッシャーが大きく、極端に慎重かつ丁寧になっていたのです。
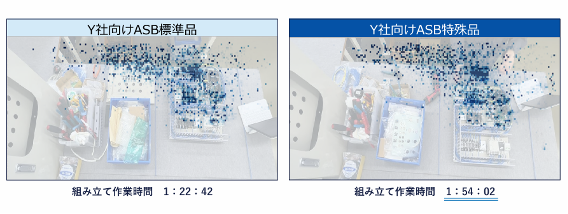
その不安を解消するため設計部門に掛け合い、設計図を書く段階で標準品と違う部分を赤い丸で囲ってもらうようにしました。赤で囲んだ箇所のみ気を付ければ良いということを示したことで、32分長くなっていたのを10分に短縮することができました。これも特別なシステムの導入や基幹システムの改変は不要でした。誰でも思いつく本当に簡単なことです。
ただ、生産現場ではチーム化されておりプロセス単体の視点が強く、全体視点が持てなくなる環境になっています。今回、設計部門の手間は確かに少し増えます。ですが全体を考えると大きなコストダウンにつながります。デジタル改善の最大のメリットは効果を明確に示すことができることです。
動画分析な単純に見えて、リソースやノウハウが必要なので、東洋電装では動画分析業務も手掛けています。ほぼ全ての動きを解剖して定量化するので、納得感や自信をもってDXを進めるきっかけになります。今までなんとなく疑問に思っていた非効率なやり方も、数値のもとにあぶりだされるわけです。社内の決裁も早くなるかもしれませんね。
また、ノーコードアプリによるデジタル改善支援についても我々がサポートできます。絶対に会社・現場を変革させることができます。デジタル改善がボトムアップで連鎖する組織変革こそがまず製造業が目指すべき姿ではないでしょうか。
【著者】
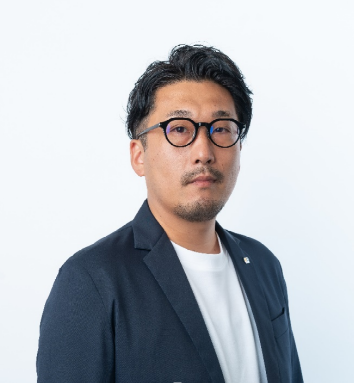
越智 稔(おち みのる)
東洋電装株式会社
制御盤システム事業 事業部長
1984年愛媛県生まれ。制御盤の設計としてキャリアをスタートし、13年間エンジニアとして国内向けだけでなく海外向けのプラント関係制御設計及びシステム開発経験がある。PLC-HMI-SCADAの開発経験も多く、ロックウェル・オートメーションやシーメンスの開発経験と複数カ国の現地でのコミッショニングを経て技術力を高めた。更に欧州向けのIEC60204-1に準拠した設計によるCEマーク取得パネル、UL508Aに準拠したUL認証パネル設計を多く行った経験がある。現在は制御盤製造の事業運営と自社DX推進及び中小製造業のDX推進をサポートする新規事業を産官学連携で立ち上げ、システム開発統括及びフィールドサポートを行っている。