製造業のDXにおける課題は多くあります。人材不足や予算の制約などもそうですが、DXの前提となる「データ」を集められていない、もしくはデータはあるものの活用できていないケースが挙げられるのではないでしょうか。
前回の記事では担当者に依存していた備品の在庫管理・発注業務を誰でもできるようにした東洋電装の事例を紹介しました。
では備品がなくなりそうなとき、発注すべき最適な数量やペースはどれくらいなのか。DXの効果を飛躍的に高める「データドリブン」の考え方について解説していきたいと思います。感覚や経験ではなく、データに裏付けられた合理的な判断によって経営判断をすることです。
オートメーション新聞の読者の皆さんには釈迦に説法ですが、製造業において在庫管理は経営の肝です。自社製品をつくるための部品が尽きれば、工場は止まる。一方で多すぎれば、経費の膨張につながります。管理や保管のコストはばかになりません。
多くの中小製造業ではこの在庫管理について長年の経験や感覚に基づいて対応しているように思います。私がお客様企業を訪問する際は必ず、次のような質問を投げかけるようにしています。
「この部品は3か月に1回、10箱のペースで注文しているそうですが、なぜ9箱や9.5箱ではだめなのですか?」
「今までこれで回ってきたから」という答えもありますが、その個数が合っていることもあれば、もっと効率的な発注の仕方が見つかることもあります。データの整理はDXの前提になるだけでなく、AIによる機械学習や自動化にも欠かせないため非常に重要です。データがそろった会社であれば、その基盤を生かして新しい改善策やDXをどんどん導入することができます。
それでは集めたデータをもとに、どのように最適解を導き出すか。ここでも東洋電装の取り組みを例題として紹介させてください。
東洋電装では制御システムを構築するために必要な部品「タイマー」について、QRコードを活用した在庫管理システムを新たにつくりました。ローコードアプリを自社開発し、新たに入荷したときは「〇個入荷」、ストックを取り出した際は「〇個取り出し」と、各従業員のスマートフォンから入力できるようにしました。面倒な仕様では現場に受け入れてもらえないので、シンプルさを重視しました。
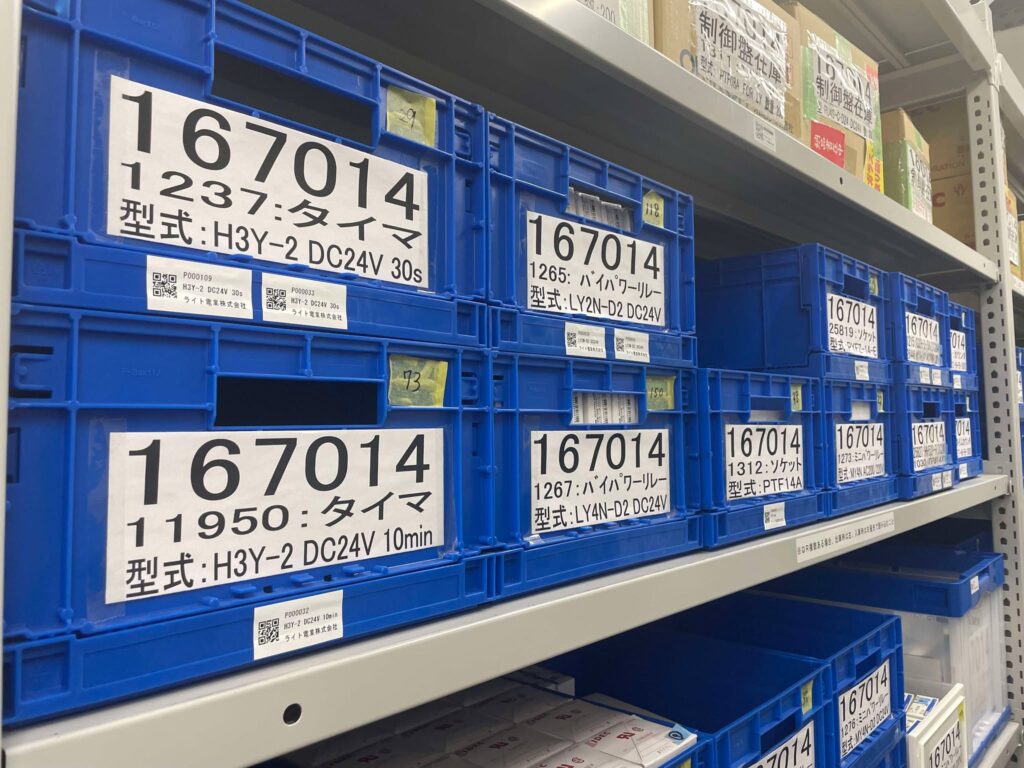
タイマーの在庫はこれまで、常に40個ほど抱えている状態でした。なぜ40個なのかという明確な根拠はなく、なんとなく「このくらいあれば安心だよね」という雰囲気からだったと思います。
ここにQRコードの新システムで取得したデータを適用していきました。タイマーの入荷・使用の状況を集計したところ、年に63個しか使っておらず、繁忙期で一気に出庫される場合でも21個でした。ということは常時40個も持っておく必要はなく、21個あればどんなに多くの注文がきても枯渇することはないことに気が付きました。
21個というのはあくまで生産に必要な分だけを考えた数字で、新型コロナウイルスのような異例の事態に備えてもう少し積み増すという判断もあり得ます。加えて部品を発注してから届くまでのリードタイムもあるので、それらを加味して最終的な水準を決めていくことになるでしょう。
実は新たなQRコードの仕組みを通さなくても、既存の販売管理システムから今回と同じデータを取ることはできました。ただ制御盤だけで数百種類ある部品のなかから選ぶので、ものすごく手間がかかります。データの海はあっても、データドリブンな意思決定ができるほど整理されたデータではなかったです。データは存在するものの、可視化されていない=何の価値もないデータは山のようにあるのではないでしょうか。
今回はQRコードを使った従業員による入力ということで、簡単な手法で価値のあるデータを取り、見える化することができました。タイマーはあらゆる制御盤に2~3個使われることが多いため、管理する優先順位は高かったです。
しかしながらタイマーの大きさは手のひらサイズ。「それが40個から21個に減ったからと言って、大したスペースの削減にはつながらないだろう」という指摘もあるかもしれません。確かにこの部品だけ見ればそうかもしれませんが、まずは気づいて着手することが何より重要なのです。他の部品、より大きな部品や数百点の在庫管理に広げられれば、保管コストをより大きく削減できるかもしれないからです。
最適な在庫水準を疑う→データを取得して検証する→実際に業務を変える。こうした一連の「成功体験」ができれば、現場から次のアイデアが出る可能性も大きく高まります。小さなデータドリブンによる改善を重ねていき、気付いたら生産現場・会社全体が「スマートファクトリー」に進化していた。それが理想のDXだと思いませんか?トップダウンでITシステムを刷新するよりも、よっぽど経済的で効果の高い手法だと信じています。
そもそも生産の現場では人手不足が深刻になっています。取り出したデータをもとに最適な水準を決めるのにも、新たに担当者が必要かもしれません。そこでAIを活用するのも大きな選択肢になります。きれいなデータがそろいさえすれば、無料ツールレベルのAIでも最適な個数を提案してくれるでしょう。東洋電装でも今後、在庫水準の判断にAIを取り入れる検討も進めています。
製造業におけるDX人材というのは、決して「最新のテクノロジーに精通している」という要素に限りません。まずはどういったデータに着目し、どう抽出し、データドリブンによる行動に落とし込むか。自社のプロセスを理解し、そうした「仮説を立てられる」人材こそが、現場を変えることができる真のDX人材だと強く思います。
仮説を立てないまま闇雲にデータを集め、ふたを開けたら使えないものだったということは往々にしてあります。生産現場のどのデータに注目すべきかは、日々の仕事のなかでは気づきにくい面もあります。
次回はどこにデータの価値があるのかに気づくための手法「業務フローの言語化」について解説していきます。
【著者】
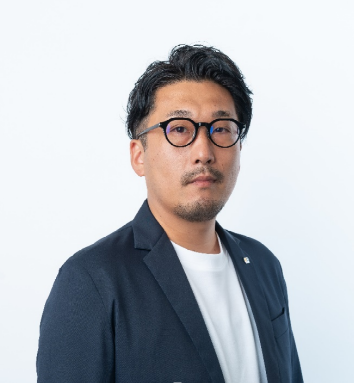
越智 稔(おち みのる)
東洋電装株式会社
制御盤システム事業 事業部長
1984年愛媛県生まれ。制御盤の設計としてキャリアをスタートし、13年間エンジニアとして国内向けだけでなく海外向けのプラント関係制御設計及びシステム開発経験がある。PLC-HMI-SCADAの開発経験も多く、ロックウェル・オートメーションやシーメンスの開発経験と複数カ国の現地でのコミッショニングを経て技術力を高めた。更に欧州向けのIEC60204-1に準拠した設計によるCEマーク取得パネル、UL508Aに準拠したUL認証パネル設計を多く行った経験がある。現在は制御盤製造の事業運営と自社DX推進及び中小製造業のDX推進をサポートする新規事業を産官学連携で立ち上げ、システム開発統括及びフィールドサポートを行っている。