制御盤の設計・製造の効率化の必要性が叫ばれて久しいですが、なかなか実現出来ていない状況があります。特に制御盤の設計は機械メーカーが行い、その製造を制御盤メーカーが担うという分業体制では、話は1企業だけにとどまらず、企業間連携になるために高いハードルとなっています。それでも制御盤は機械の頭脳であり心臓部でもあり、プロセス効率化は避けては通れない重要課題。
この課題をどうクリアしていけばいいのか? 制御盤の筐体・クーラー・加工機やITラックメーカーのリタールの代表取締役社長 新岡卓 氏に聞きました。
制御盤の設計・製造連携が進んでない現状と理由
ーー制御盤業界の現状をどう見ていますか?
制御盤を標準化して設計・製造を効率化していく必要性は以前から言われていることですが、実際には遅々として進んでいません。日本では全体最適を掲げながら部分最適のみとなっており、意思決定を根本から変えなければいけないと感じています。
ーーそもそも標準化や設計・製造連携のメリットは理解されているのでしょうか?
制御盤の設計・製造連携の話をすると「必要性は分かる」「興味がある」「確かにやらないといけない」と多くの人は賛同してくれます。しかしそこから実行出来るかどうかは別問題。進んでいないのは、人手不足を含む課題が山積みで自社プロセス改革の必要性は十分認識しているものの、不可能と感じてしまっている人が多いのだと思います。
発注者のエンドユーザーや機械メーカーの理解が大きなカギに
ーーこれを進めるにはどうしたらいいでしょう?
ピラミッドの頂上に位置する企業(本文では頂上企業と呼ぶ)がピラミッド全体のかじ取りと命運と担っています。ピラミッドは複数の小さなピラミッドを内包している意思決定構造となっており全体の動きに呼応します。そうした状況を打破するためにも、当事者である制御盤メーカーはもちろんのこと、仕様決定者・発注者であるエンドユーザーや機械メーカー頂上企業が率先して取り組むことが必要です。
日本での制御盤メーカーの立場は、ビジネス構造のなかでも末端に位置し、エンジニアリングプロセスのなかでも最後尾、と非常に厳しい立場にあります。しかも中小企業が多く、人材採用も難しく、現従業員の高齢化で事業継続が困難となってきています。
発注者を頂点とした垂直統合型のピラミッド構造では、上位に位置する企業は下層企業の実際の苦労や課題を感じにくく、実態を把握できていないケースが多々あります。そのため制御盤メーカーがどれだけやり方を変えて欲しい、改善して欲しいと要望をあげてもなかなか採用されず、事業環境が大きく変化しているにも関わらず、やり方や仕組みは従来通りで、制御盤メーカーが疲弊しているのが現況だと考えています。
全体最適が進みにくい 日本の垂直統合型ピラミッド構造
ーー世界でも似たような状況ですか?
欧州では水平分業が進んでおりで、発注者となる機械メーカーと制御盤メーカーの関係性は穏やかに結びついており、ノウハウの蓄積とソリューション提案がし易い。故に事業構造の合理化や全体最適がしやすい、標準化を導入しやすいなどの違いはあります。
日本の高度経済成長期期であれば、垂直統合型ピラミッド構造であっても、多数の制御盤メーカーと多くの労働者によって、大量生産を賄う事が出来ました。だから多少の無理があっても、ピラミッドに属している企業がみな繁栄でき成長が可能でした。
しかし今日のような経済・事業環境、更に制御盤メーカーの人材が不足しているなかでは、状況に適した形に全体のプロセスを変えていく必要があると考えます。
幸いにもまだ制御盤メーカーがなんとか頑張っているおかげで、制御盤が調達できなくなる、自社の機械が作れなくなる、生産ラインが完成しない、などという危機的状況までは至っていません。しかし制御盤メーカーが要求された仕様・品質や納期を確保できなくなるリスクは年々高くなっています。だからこそ仕様決定者であるエンドユーザーや機械メーカー頂上企業が制御盤メーカーの置かれている立場と実態をもっと理解して頂きたい。ピラミッド全体で危機感を共有し、仕様決定者頂上企業の率先した意思決定により全体最適をピラミッドに落とし込む事が極めて重要になっているのです。
発注者の経営層レベルでの理解と実行力も重要
ーー確かに下から変えていくというのは難しいものがあります
仕様決定者頂上企業・発注者のなかでも、特に全体を俯瞰する立場の人が全体最適や標準化を理解し、主導できるかどうかも大きなポイントです。
機械の重要部品である制御盤の設計・製造プロセスを変革するには、設計と製造部門のみならず、購買部門やIT部門も含めて協議し、方向性を取りまとめなければなりません。さらに全体のバリュー・チェーンに属する外注先や協力会社をも含めた全体最適を設計して段階的にデジタル化を導入しての生産性を高めることが求められます。
部門間の横串を指すチームを作ったり、調整力がある人に任せるというケースがありますが、各部門がサイロ化している日本の企業文化のなかで、いくら社長直轄の組織を作ったり、全社のプロジェクトとして大義名分を与えたとしても、部門をまたいでの合意形成は至難の業。どんなに能力がある人がやったとしても限界があると思います。
やはり経営層が経営課題として直接的に取り組むことが必要です。
設計・製造連携がサプライチェーンを強靭化する
ーー機械メーカーのサプライチェーンの強靭化ですね
機械メーカーはエンドユーザーのニーズを汲み取って自社製品の多品種化を進めていますが、制御盤が標準化されないまま多品種化していることで制御盤メーカーは労働者不足のなかでその対応に追われ、必要な生産数・納期で完成させる事ができない状況になってしまっています。
だからこそ機械設計の段階で、工作機械メーカー側がある程度のパターンで制御盤設計を想定した設計プロセスに変える事で後工程がスムーズになり最適化に向かいます。こうすることで制御盤メーカーの負担を軽減でき、今まで通りのやり方で制御盤を製造し続けられるようになり、サプライチェーンの強靭化ができるのです。
例えば同じ機械向けの制御盤であっても、端子台は海外の輸出向けはプッシュイン、国内は丸端子・Y端子のケースなどがあります。このようなダブルスタンダードをなくし、プッシュインに統一するなど、機械メーカーがエンドユーザーに訴求して実現できれば内部コストを下げ、生産性が向上します。
制御盤の設計・製造連携と「箱は部品」を訴求
ーー制御盤の設計・製造の効率化に向けて御社はどう対応していきますか?
これまで通り制御盤の設計・製造連携のメリットと「箱は部品」であることを地道に訴求していきます。
機械メーカーも制御盤メーカーも、制御盤の箱は板金で作るものという認識が根強く残っています。そのため板金塗装工程や製缶工場を自社に保有または外注し、コストと時間、手間をかけ、必要に応じULなどの国際規格を取得しています。
人手不足や困難な事業継続性によって中小の板金塗装企業も年々数が減るなか、自前の筐体製造は全体最適の観点から採算に見合わず、リスクにもなります。だからこそ「箱は部品」と発想を転換して割り切り、カタログから標準品を選んで調達することも必要なのではないでしょうか。EPLANの電気設計CADを導入し3Dレイアウトを活用できるようになると、箱は板金図が不要で3Dデータから選ぶだけになり、制御盤の設計と調達、製造の効率化にもつながります。
設計・製造連携を体感できるアプリケーションセンターを小田原に開設
さらに、製造工程の効率化・自動化のためのツールとしてRAS(Rittal Automation Systems)があり、その提案も強化していきます。
神奈川県小田原市の小田原プロダクトサポートセンターに設計・製造連携を体感できる「リタールアプリケーションセンター」を開設します。これまでも設計・製造連携や自動加工機の提案は行ってきましたが、日本国内でその実例を見せられる機会がなく、ようやく日本で実際にご覧いただける様になります。センターには全自動電線加工機「ワイヤターミナル WT」を導入し、筐体への穴あけ・切断の自動加工機「Perforex」も設備更新をして、実際にEPLANで作ったデータを加工機に送って自動加工をする設計・製造連携のデモを行うことができます。正式オープンは2024年度中を予定しています。
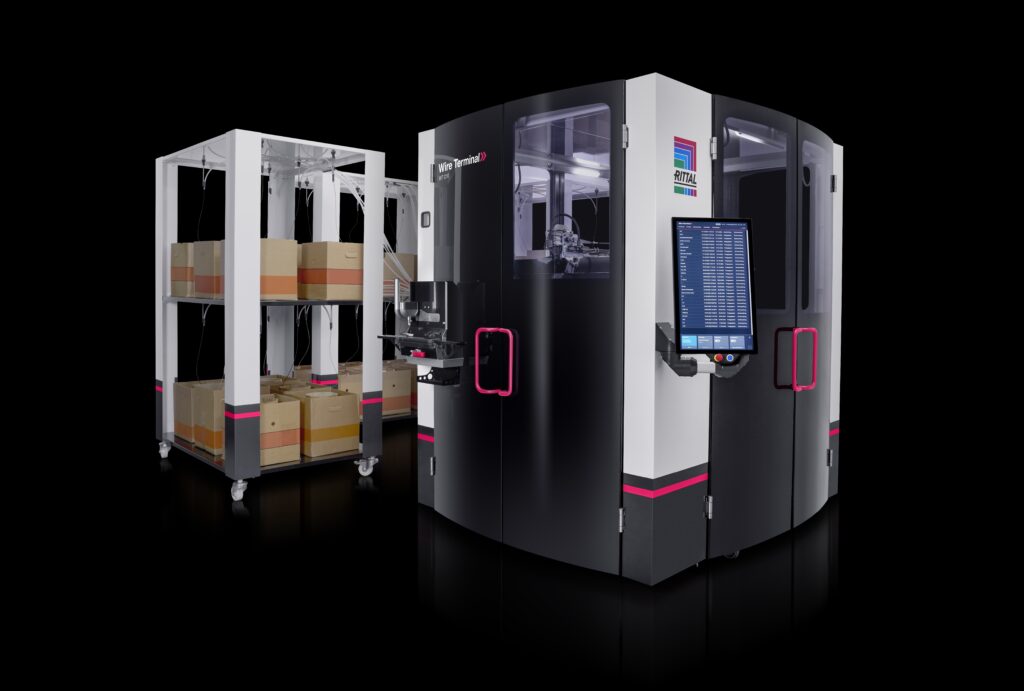
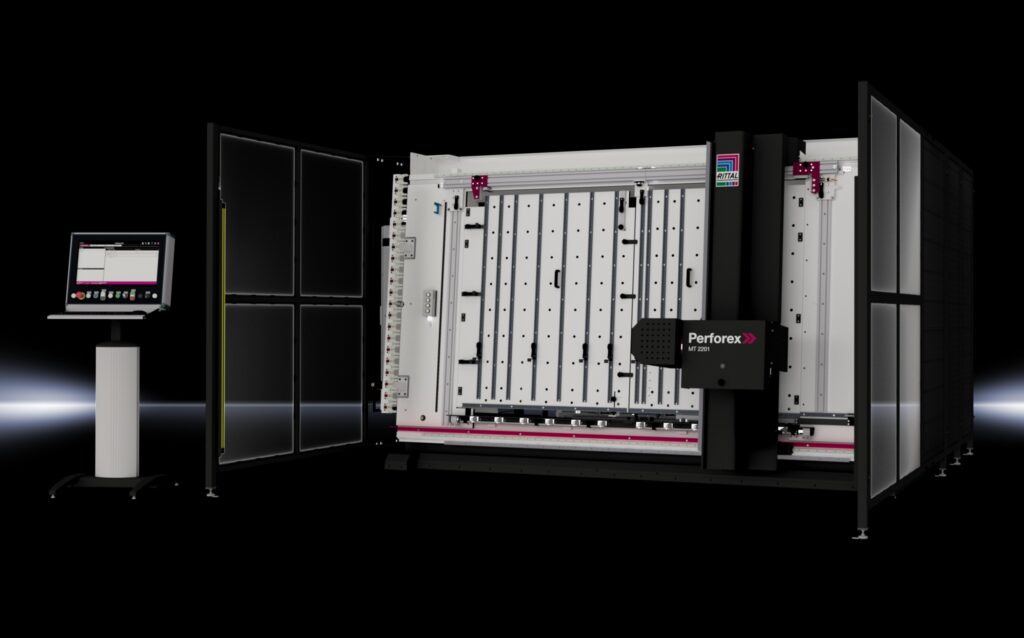
スマートマニュファクチャリングを実現する3つのデジタルツイン
ーー今後に向けて
当社はスマートマニュファクチャリングを実現するためには、3つのデジタルツインが必要だと考えています。ひとつは、制御盤の設計データをもとにデジタルデータを作り、それを使って設計から製造・運用を効率化する「オートメーションツイン」、ふたつ目は、生産ラインや機械のメカ設計データ、電気設計のデータを統合し、さらにはPDMやERPなどとも連携して、製品構成やその製造プロセスまでカバーする「プロダクトツイン」、そして三つ目は、据え付け・立ち上げ後の現場で動いている時の稼働データによる「プロダクションツイン」。この3つのデジタルツインを進めることで、機械や生産ラインの立ち上げも早くなり、安定稼働・生産性の更なる工場が可能になります。
現在、欧州ではオートメーションツインはほぼ整備され、機械CADのメカ設計データもすでにあってプロダクトツインへのデータ統合も実現できる環境にあります。制御する側のオートメーションツインと、制御される側のプロダクトツインを組み合わせ、仮想空間上でシミュレーションできる環境になっています。これにより設置や据え付け、調整のスピードアップを図る事が可能です。
さらにこれからはプロダクションツインを使って、仮想空間上で実際に稼働している装置の状態を監視し、更なる生産性向上や生産ラインの変更などをシミュレーション出来るようにする段階に入っています。あらゆる工場がプロダクションツインになれば企業間の生産をも全体最適化が可能となる社会が来るかもしれません。それにより製造コストやエネルギーコストなどを社会全体でミニマムにできるようになります。
現在、日本ではオートメーションツインで立ち止まっている状態で、それを先に進める為にも企業単体だけでなく、制御盤の設計・製造に関わる全ての企業群が全体最適に取り組む必要があります。高いハードルですが、日本が今後もものづくり国家として存続するためにも避けては通れませんので、当社はそれを支援していきたいと思います。
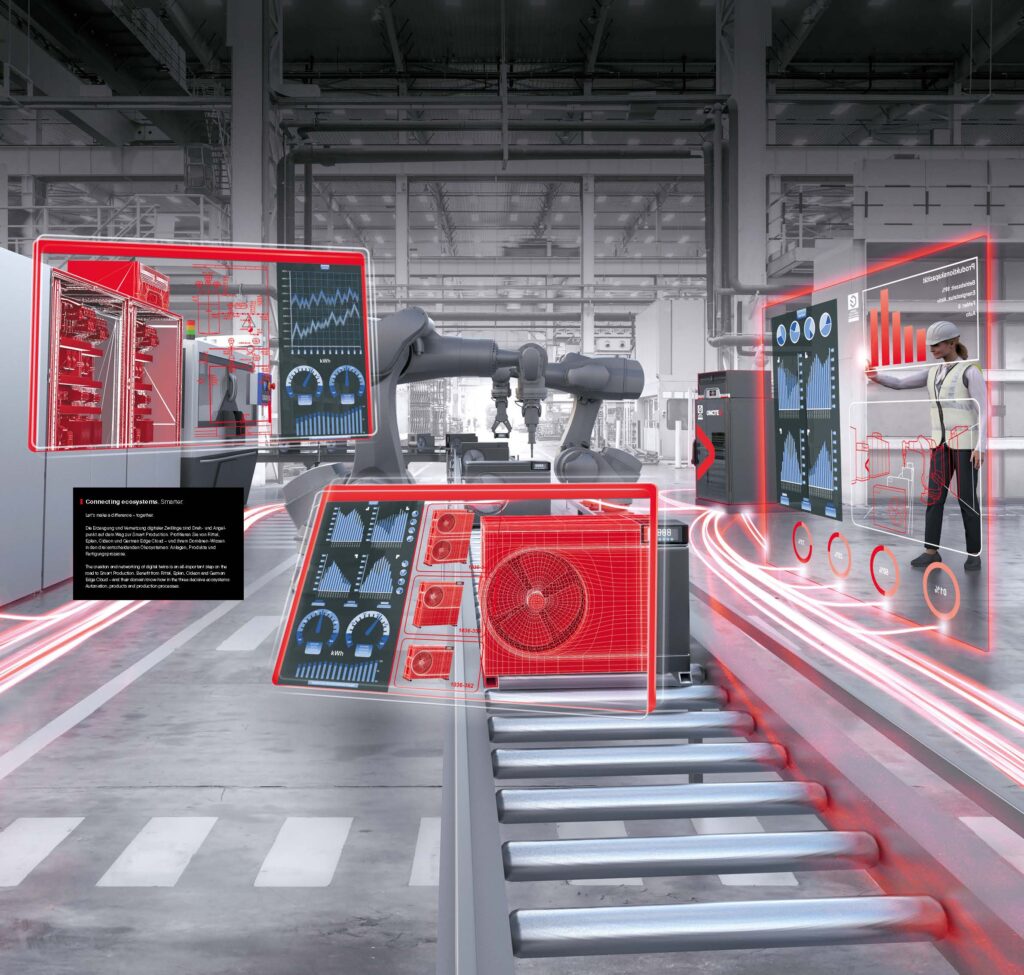