ナカサク(滋賀県湖南市)は、1926年創業のオーダーメイドを得意とする超老舗の産業機械メーカー。受注案件は基本、オーダーメイドのため、要件も技術もさまざまな製造装置に対応しなければならず、そこで培った技術対応力が最大の強みとなっています。
人手不足や働き方改革で昔のようにはいかない時代の流れのなか、2020年から制御盤の設計・製造の効率化・標準化をスタートし、成果を上げています。
その取り組みについて話を聞きました。
目次
- 1 オーダーメイドの製造装置が得意
- 2 100年蓄積した技術力
- 3 電気設計の標準化・効率化をスタート
- 4 電気CADをECAD DCXに更新
- 5 検図作業を大幅削減
- 6 ECAD Libraryをベースに自社用マスタを整備
- 7 マクロ活用、3D化でさらなる設計業務の効率化
オーダーメイドの製造装置が得意
--御社について教えてください
当社は1926年創業のオーダーメイドで生産用機械を設計・製造する産業機械メーカーです。
「?×!=∞」の企業メッセージのもと、お客様の課題に対し、提案力と開発力、製造力で解決し無限大の価値を生み出すことを目指しています。
大手のガラスメーカーや鉄鋼メーカーが主な顧客で、その工場で使われる製造装置を作っています。それ以外にもプラズマディスプレイパネルや太陽光発電パネル向け装置、電池向けフィルムなど、その時代に合わせて全国から相談が寄せられ、最近はEV関連の製造装置も手がけています。
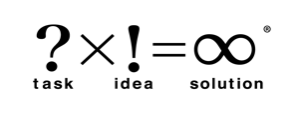
100年蓄積した技術力
--2026年で創業100周年です
もともとは創業者が兵庫県尼崎市でガラスメーカーの設備や装置メンテナンス業で創業し、そこから保全業務で必要となる部品や治具の製造のために工作機械を導入して部品製造に取り組むようになりました。そして自社でお客様向けの製造装置へと事業を広げ、今に至ります。
この100年の間に蓄積された技術力が一番の強みです。ガラスと鉄の製造装置では使われている技術や求められる要素は異なり、それ以外にも様々なオーダーメイドの産業機械を手がけてきた実績と技術を培ってきました。
また機電一体で、機械と電気をひとつの社内でできるのも特長です。社内に営業部門はなく、機械と電気の技術者が技術営業となってお客様の話を聞き、提案し、お客様と一緒にオリジナルの機械を作ることができます。
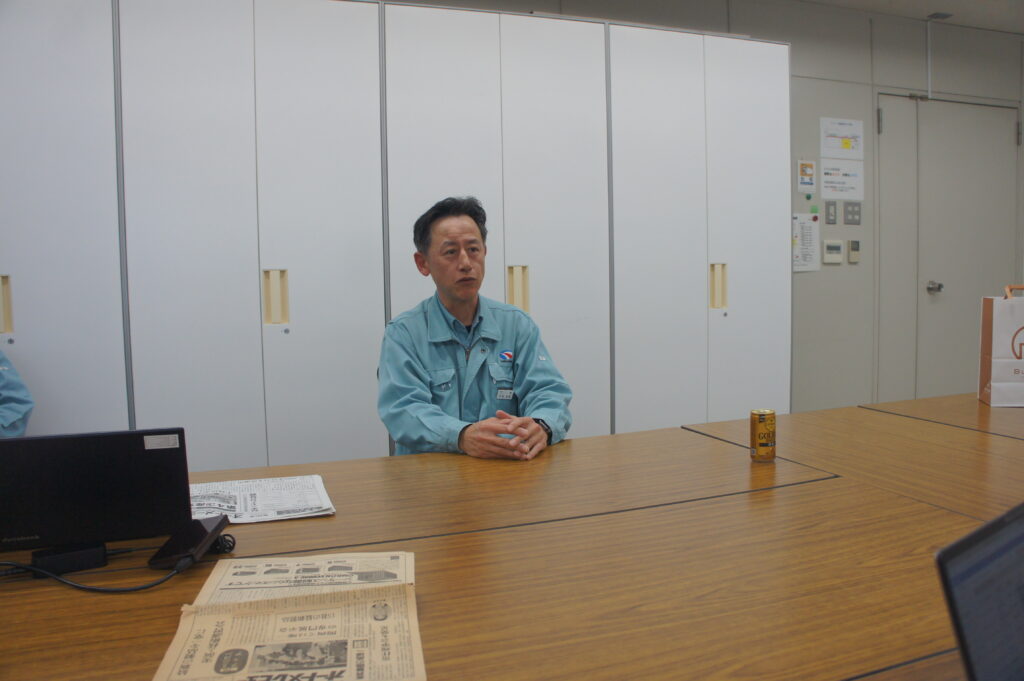
--電気設計部門について教えてください
10年以上前の組織変更の時、設備技術部として社内保全を担当していた部署に、設計部門から電気設計を担当していたスタッフが加わり、社内の電気関連を担当する電機セクターとなりました。いまは14人が在籍し、うち13人が設計を担当しています。
制御盤の設計・製造については、社内で電気設計を行い、その後、組み立てと配線はパートナーの制御盤メーカーに担当してもらっています。電気CADはECADソリューションズのECAD DCXを利用しています。
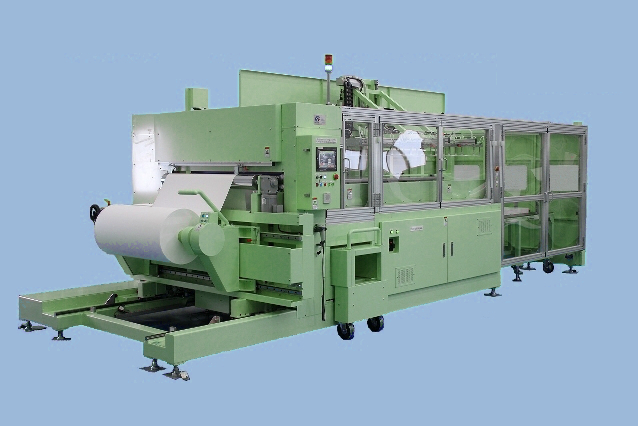
電気設計の標準化・効率化をスタート
--制御盤の設計・製造の効率化について
2020年に経営陣から各部署に、自部門の重要な中期取り組みを設定し、ゴールと行動計画を検討実行する機会をいただき、電機セクターは「電気設計の標準化・効率化に取り組むこと」を目標としました。
当時、仕事ができる人とできない人の就労時間と作業量の差が大きくなっていて、できる人ばかりに仕事が集中して長時間残業が酷いことになっていました。ちょうど時間外労働の上限規制に対応しなければならないタイミングでもありましたし、標準化を通じてスタッフ全員のスキルアップも必要だったため、これを部署目標として取り組みはじめました。
電気CADをECAD DCXに更新
--具体的にはどんな取り組みをしたのですか?
電気CADを更新し、それまで使っていたECAD dioからECAD DCXを導入しました。
これまでのECAD dioでの設計は、必要な部品を配置して、線をつなぎ、図面を描くだけでした。そのため部品の型式が入っていなかったり、回路図に記載されているものが外形図に
なかったり、そのために部品の買い忘れが発生したりと多くの抜け漏れがありました。後工程の制御盤メーカーから問い合わせされることもあり、そうしたミス対応に時間を取られることも多くあり、非効率でした。
それに対しECAD DCXでは、回路図と外形図の整合性を自動でチェックができ、部品データも部品マスタから呼び出して図面に配置できるので、以前のようなミスを減らすことができると思いました。
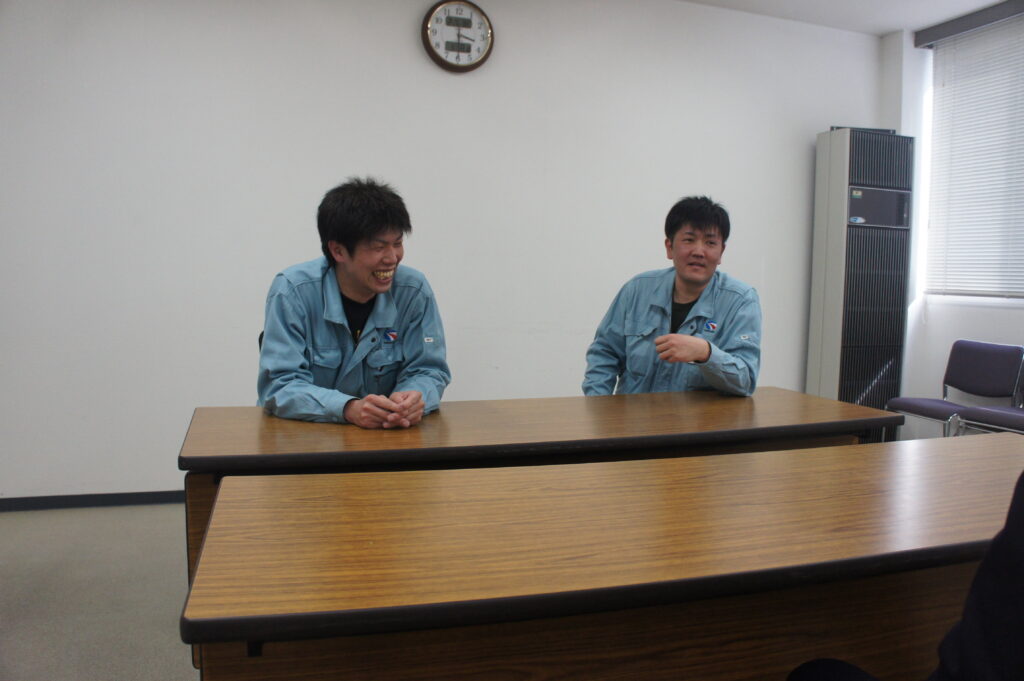
検図作業を大幅削減
--導入の成果はいかがでしたか?
導入当時はコロナ禍真っ只中だったので、対面できめ細かく使い方のレクチャーを受けられなかったこともあり、立ち上げには想定以上の時間がかかってしまいました。それでも、検図した際の図面の抜け漏れやズレといったミスは大きく減り、図面や部品表の作成も効率的に行えるようになりました。
残業も明らかに減りましたし、制御盤メーカーから図面の不具合に対する電話もなくなり、社員にも制御盤メーカーにもお客様にもお互いにウィンウィンになっています。
また、これまでは当社で板金図面を作成し、仕入先に日東工業のキャビスタを使用してもらって標準キャビネットを調達していましたが、手作業で穴データを入力しなおしていたため、穴位置の間違いなどのミスが発生していました。キャビスタ連携機能を使用することでミスは完全になくなり、キャビネットの手配も格段に楽になりました。
ECAD Libraryをベースに自社用マスタを整備
--業務の標準化については
以前は部品のシンボルや型式などの部品情報の表現に対する社内ルールはゆるく、設計者によって統一感がなく、それによる非効率やミスも起きていました。それに対し、今後は全員が同じ部品データを使うことで業務を標準化したいと考えて取り組みました。
ECAD DCXを導入する際、これまで使用した部品と、ECAD Libraryに登録されている部品データをもとに独自の部品マスタを作りました。部品マスタには、これまで使ったことがある部品の数千点のデータが入っています。設計者は必ず部品マスタからデータを引き出して図面や部品表を作るようにルール化し、さらにデータの編集や追加は管理者のみが行えるようにしています。
部品マスタと運用ルールを標準化したことで、設計者は図面を作ることに集中でき、部品マスタのメンテナンスもスムーズに運用できるようになりました。
マクロ活用、3D化でさらなる設計業務の効率化
--今後に向けて
今後は部品マスタを更に充実させ、マクロ機能を活用して設計の効率化・自動化にチャレンジしていきたいと考えています。
例えば、熱対策のため制御盤の温度上昇を調べる際、今まではそれぞれの部品の発熱量を調べ、それを合算して導き出していましたが、部品マスタに各部品の発熱量をデータが登録しておけばマクロで簡単に制御盤の発熱量が算出できるようになります。部品マスタの拡張とマクロの活用を進めることで、もっと色々な効率化が実現できると思います。
また3Dデータの利活用にも取り組みたいと思っています。当社で設計した制御盤をそのまま製作した際に部品の干渉が起きてしまい、制御盤メーカーが組み立て・配線の際に手を加えてくれたおかげで完成したというケースが時折あります。自分の頭の中で描いている図面と実際の制作物である制御盤とのギャップをなくすためには、設計段階における事前検証が必要です。特にこれから制御盤の小型化が更に進むと、事前検証を更に緻密に行う必要があります。そのためにも3D化を進めていきたいと思っています。
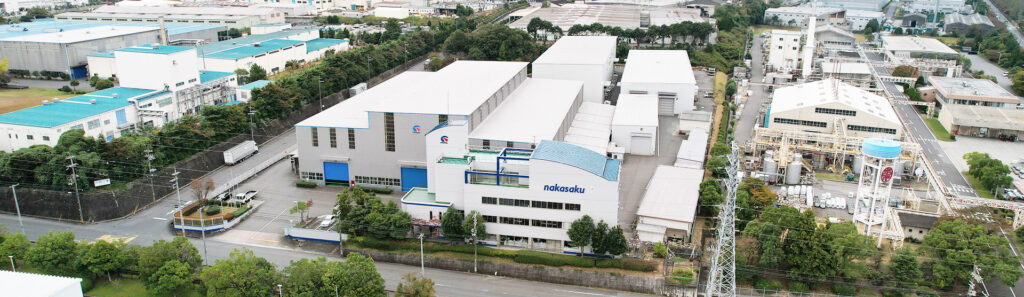