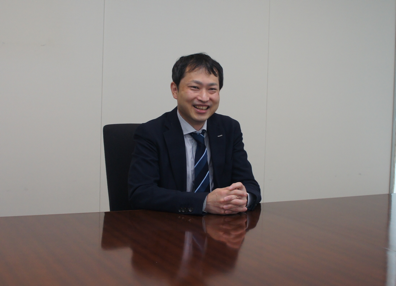
インダストリアルオートメーションビジネスカンパニー 検査システム事業本部 X線検査システム事業部 事業部長 村上清 氏
オムロンというとセンサやリレー、PLCなど自動化に必要な部品を開発・製造する制御機器メーカーのイメージがありますが、検査システム事業本部は完成品の「検査装置」を取り扱う異色の部門となります。実装基板のはんだ付け品質を調べる外観検査からはじまり、そこから派生して基板や部品の寸法を測る寸法検査、紙やフィルムなどロール状の原反の表面を調べる表面検査などに向けた画像検査装置を展開。特にX線CTスキャンによる高速で精密な検査技術はインラインでの検査を実現し、高く評価されています。
そして現在、技術の進化が激しく、生成AIやEV、再生可能エネルギー、カーボンニュートラルなど各方面で需要が急拡大している先端半導体やパワー半導体向けに特化した検査装置を開発し提案を強化しています。
そんなオムロンの検査システム事業の現在の取り組みについて、インダストリアルオートメーションビジネスカンパニー 検査システム事業本部 X線検査システム事業部 事業部長の村上清 氏に聞きました。
ヘルスケア事業の画像処理技術を応用
ーーもともと検査システム事業はどのように始まったのですか?
1980年代にある電機メーカーから電子基板の部品実装の検査を自動化したいという相談があり、ヘルスケア事業の研究開発部門が開発した赤血球の数を数える画像処理技術を利用して1987年に電子部品のはんだ付け、表面実装の検査装置を開発したのがスタートです。そこから2000年頃にガラケーやスマートフォンの実装部品で1005(1.0×0.5mm)サイズのものが出てきて、このサイズでは人での検査が難しいということで需要を獲得して事業を拡大。さらに2008年頃には、ある自動車部品メーカーのお客様から「はんだ付けの品質検査について、外観を見ただけでは分からない。はんだ内部の接合状態を確認したい」との声を受け、X線を使った検査装置を開発・提供を始め、いまに至ります。
X線CTスキャンによる精密検査を高速で実現
ーー検査装置メーカーが数多くあるなかで、御社の強みや特長は?
一番の特長は、X線のCTスキャンによる正確な検査を高速ででき、且つ装置を生産ラインに組み込んでインライン検査ができることです。
例えば病院で体の検査をする場合、医者ははじめにレントゲンで2Dの透過画像を撮影し、それを見て大まかな検査をします。それから画像に影があった場合、精密検査としてCTスキャンで体の輪切り画像を何枚も撮影して細かく検査します。こうすることで患者の体の内部で何が起きているのかが分かり、治療法・対処法を考えることができます。
製造業におけるX線検査もこれと同様で、当社はレントゲンではなく、より精密な検査ができるCTスキャンにこだわっています。
さらに、良品・不良品を自動判定する点がポイントとなります。そのため、お客様の生産タクトに合わせられるように、検査速度の高速化も実現させました。高速化の実現にあたっては、装置を構成するコンポーネンツに自社の強みである制御機器や、自社開発の検査アルゴリズム、最新のGPUボードを駆使しています。制御の専門企業としての技術を極限まで盛り込み、インラインで全数検査できるレベルまで仕上げ、メンテナンスも簡単に行えるようにしています。
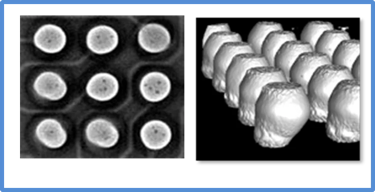
先端半導体、パワー半導体向けなど3タイプの新機種を
ーー精密なCTスキャンによる検査を高速でできるということですね
そうです。そしてこのたび新モデルとして3機種を発表しました。
1つ目の表面実装基板(SMT)用の「VT-X750ーXL」は、基板サイズの大型化に対応したモデルで、5Gや6Gの通信基地局向けの基板やEVバッテリのコントローラ基板などのアプリケーション向けになります。
2つ目の「VT-X850」は、IGBTモジュールやインバータモジュールなどパワー半導体向けのモデルになります。大型で厚さがあるもの向けに重量搬送の機構や高出力のX線を使ったものとなります。
3つ目は半導体の先端パッケージ向けの「VT-X950」で、超マイクロフォーカスX線源で、高速性を維持したまま分解能を高めたモデルです。従来機種が1画素3ミクロンのところを、VT-X950では1画素0.2ミクロンの分解能で、半導体の先端パッケージの微細なところまで検査できるようになっています。
最新半導体のチップレット構造に対応するVT-X950
ーー次世代通信、パワー半導体、先端半導体と話題のトレンドに対応する機種ですね
電子部品、半導体、実装技術の進化にともなってアプリケーションも広がっています。
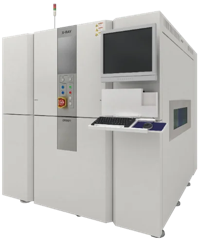
例えば、VT-X950がターゲットとする先端半導体について言えば、ムーアの法則が限界を迎え、最先端の半導体の研究開発費や生産装置も高額になり、よりいっそうの歩留まり向上が課題となっています。そこで、性能と歩留まり向上の両方に効く「チップレット」という工法が注目されています。チップレットは、メモリやロジックなど異なる種類の半導体を並べ、さらにそれを積層して封止して1つの半導体パッケージとしたもので、半導体の構造自体がこれまでとは大きく異なります。チップレットを作るためのはんだ付けも200ミクロンから40ミクロン、8ミクロンと微細化し、その接合検査にも超高分解能が必要とされます。
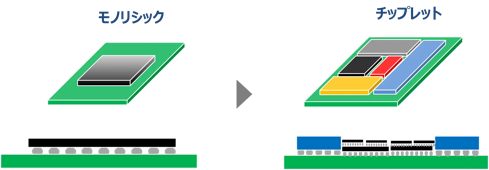
VT-X950はチップレットの半導体パッケージの検査装置として開発し、チップレットで使われるμBumpやC4Bumpのはんだ付け品質を可視化できます。現在は人が解析装置を使って半自動で検査を行っていますが、VT-X950はインラインでほぼ人が介在せずに自動で検査が行えるようになっています。
またチップレットになると製造工程も前工程と後工程だけでなく、その中間の「中工程」の割合が大きくなってきます。中工程ではウエハも扱うためクリーンルーム対応も必要となり、VT-X950ではVTシリーズとして初めてクリーンルームに対応しました。
パワー半導体モジュールの内部も見通すVT-X850
ーーパワー半導体向けの機種もあります
VT-X850は、はんだの接合面積や内部の気泡の有無などの検査に使われ、自動車部品メーカーのお客様に、インバータやeAxleのようにモジュール化された製品やそのなかのIGBTやパワーカードなどの検査で引き合いを多くいただいています。
接合面積は電流容量、電圧容量に関連する重要な要素で、不十分だと性能が十分に発揮できなくなります。例えばEVでは充放電の時間が倍かかるようになったり、走行距離が短くなったりする原因になります。またはんだの中に気泡があると発熱の原因になり、発熱を防ぐために性能を落とさなければならなかったり、耐久性が犠牲になって故障の原因になったりもします。そうしたものを検査で見つけ出すことができます。
チップレットもパワー半導体も性能が上がってユーザーにとっては製品の使い勝手が高まる半面、構造が複雑化し、モノづくりの観点では外観や機能検査では品質が担保しきれない部分が多くなっています。そうしたなかで内部まで細かく見られるX線CTスキャンのニーズはより拡大していくと考えています。
専門スキルは不要。AIで設定やプログラム生成をサポート
ーー画像処理、しかもX線CTスキャンというと設定や操作が難しそうなイメージがあります
そのために独自開発のAIが、熟練作業者のような専門スキルがなくても検査プログラムの作成ができたり、人による設定のばらつきを軽減する様アシストしています。
従来は、画像を白と黒に単純化する2値化という方法ではんだの位置やクラックなどを抽出して手入力で設定していました。新しい方式では、あらかじめはんだの位置を指定しておくと、設定いらずでAIが抽出してくれるようになっています。
これから熟練者が減って人手不足が進むことを見越して機能を搭載して対応しています。
検査工程から歩留まり改善をサポート
ーー今後に向けて
半導体や電子部品、基板実装では歩留まりをいかに上げるかが重要とされています。
規格通り作られたチップを電極につないでも動かなかったり、性能が出なかったりした場合、外観では異常がなかったとしても、実はどこかではんだブリッジや接合内部に気泡ができていたりすることがあります。X線CTスキャンを使うことで見えなかった不良が見えるようになり、発生の原因究明に役立ちます。
半導体は微細化が進んで作るのが難しくなり、構造の複雑さも増しています。そのなかで装置から出てくるデータだけで歩留まりを改善するのは限界があります。だからこそ、作られたものを定点観測し、そこから得た情報でフィードバックをかけることで生産ラインの品質をコントロールでき、歩留まりを改善できるようになります。検査装置といっても単にOK・NGの判定をするだけでなく、検査で得られたデータをフィードバックすることにも力を入れていきます。
また当社はロボット事業も展開しており、人手不足が進むところに全社を挙げて省人化や自動化ソリューションを展開していきます。
https://www.fa.omron.co.jp/product/inspection-system/sji-inspection-system/axi